Introduction: The Unsung Hero of Globalization
The shipping container stands as the fundamental, standardized unit of value underpinning the modern global economy. While often viewed as a simple steel box that “made shipping cheap,” this narrative must be expanded to position it as a revolutionary platform technology—what the silicon chip is to computing, the container is to logistics—enabling the complex, long-distance supply chains of globalization. The pre-container “break-bulk” era was characterized by high labor costs, slow turnaround times in ports, and significant cargo losses.1 This inefficient environment set the stage for the transformative impact of the container.
The true genius of the shipping container lies in its uniformity. This standardization, codified by the International Organization for Standardization (ISO), was the key that unlocked immense efficiencies in intermodal transport (ship, train, truck).1 The purpose of this report is to deconstruct this seemingly simple object and reveal the complex ecosystem of material science, manufacturing, economics, logistics, and regulation that supports it. This analysis will show that the container is not just a means of transport, but an infrastructure that has reshaped global trade itself.
Chapter 1: Anatomy of a Container — From Raw Steel to Global Standard
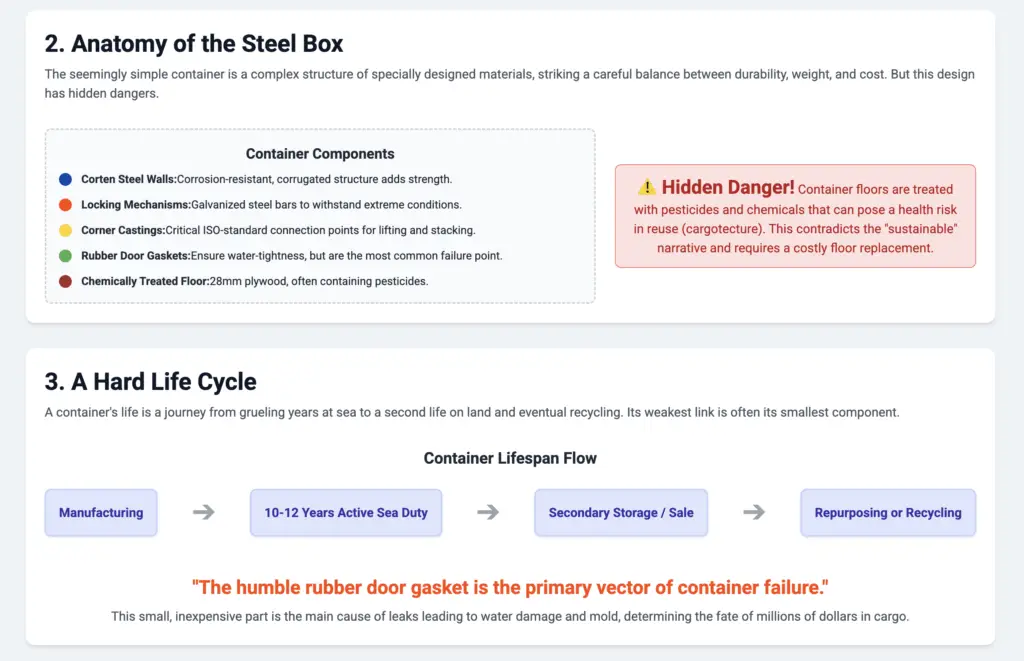
This chapter deconstructs a shipping container with the material and process details necessary to understand its physical structure, durability, cost, and lifecycle limitations. This detailed information provides an ideal foundation for technical diagrams and cross-sectional visuals.
1.1 Material Science: The Indispensable Corten Steel
The primary material used in the production of shipping containers is Corten steel, a special weathering steel alloy chosen for its high tensile strength and superior corrosion resistance. This is not just any steel; it is formulated to form a stable, rust-like protective layer when it comes into contact with the atmosphere, which inhibits deeper corrosion. This self-protecting feature is critical for containers to withstand the harsh conditions of sea voyages.
The manufacturing process begins with large rolls of this steel. The rolls are unrolled, flattened, sandblasted to remove contaminants, and primed.4 The sheets are then cut to precise dimensions using hydraulic shears or laser cutters and fed into massive press machines that give them the characteristic corrugated texture of containers and increase their structural strength.
This corrugation process not only provides an aesthetic texture but is also a critical engineering feature. These grooves significantly increase the structural rigidity and resistance to bending of the wall panels. This allows for the use of thinner (and therefore lighter and cheaper) steel sheets without compromising the shipping container’s ability to be stacked and withstand immense forces. This is a fundamental design trade-off between material cost, weight, and strength. A flat sheet of the same thickness would be much more prone to buckling under the pressure and torsional forces generated during stacking and transport. Corrugation increases the panel’s moment of inertia, enhancing its resistance to bending by acting like a series of integrated I-beams. This allows manufacturers to achieve the required structural integrity specified in ISO 1496-1 tests using less steel. However, this design has a disadvantage: the grooves create troughs where moisture can collect and potentially accelerate localized corrosion if the protective paint coating is breached. This creates a maintenance challenge throughout the container’s life.
1.2 The Manufacturing Blueprint: A Symphony of Man and Machine
Contrary to popular belief, shipping container manufacturing is not a fully automated process. It is a mix of heavy machinery and a significant amount of manual labor, especially skilled welding.4 The process follows a clear sequence:
- Floor Frame Assembly: First, the foundation is created by welding together heavy-duty I-beams or C-channels to form a sturdy base.
- Wall and Door Panel Assembly: The corrugated steel sheets are welded to tubular steel frames to form the wall panels and doors.
- Box Assembly: The doors and wall panels are lifted by crane and welded to the floor frame, followed by the corner posts, and finally, the roof panel is welded into place. In modern factories, some of this welding process may be automated with robotic arms to ensure consistent, airtight seals that meet ISO standards.
- Finishing: The assembled box is sandblasted again, then primed and painted with multiple coats of industrial-grade, marine-grade coatings to protect against salt, water, UV rays, and chemical exposure.
1.3 The Unseen Foundation: The Floor and Its Hidden Dangers
The floor of a standard container is not steel, but typically 28mm thick multi-layered marine-grade plywood. The wood is selected from durable tropical hardwoods like Keruing or, increasingly, bamboo. Six plywood panels are usually used to floor a standard container, and they are screwed directly into the steel cross-members of the floor frame.
The critical detail of this process is that the plywood is pressure-treated with a chemical cocktail containing insecticides and fungicides (anti-rot agents) to ensure longevity and prevent pest infestations during international transport. While these chemicals are FDA-approved for their intended use, their presence is a significant and often overlooked issue.
This chemical treatment of container floors poses a significant hidden liability and health risk for the burgeoning “cargotecture” (shipping container architecture) industry. Pesticides and other chemicals can off-gas into the interior space, especially when heated, creating a health hazard for occupants if not properly remediated. This creates a direct conflict with the “eco-friendly” and “sustainable” narrative of cargotecture , which is complicated by this hidden toxicity. Proper reuse of a shipping container requires the costly and wasteful removal and replacement of the entire original floor, which undermines some of the sustainability claims. This is a vital detail for anyone considering a container conversion project.
1.4 The Gatekeepers: Doors, Gaskets, and Locking Mechanisms
Shipping container doors are made from the same corrugated steel as the walls and are encased in a square steel tube frame. They are equipped with galvanized steel locking bars, cams, and keepers designed to function in extreme temperatures.
The most vital and failure-prone part of the door assembly is the rubber gasket or seal that lines the edges. These gaskets are necessary to create the wind and watertight (WWT) environment that protects the cargo. Over time, these gaskets degrade due to UV exposure, temperature fluctuations, and physical wear, becoming brittle or dislodged and leading to leaks.
This humble rubber door gasket is the primary vector of container failure, directly leading to the most common types of cargo damage (water damage, mold) and compromising the container’s structural and commercial value. Its maintenance and inspection are disproportionately critical to the container’s operational success. While many sources highlight door gaskets as a key component for waterproofing , damage reports list “Worn or Damaged Door Seals and Gaskets” as one of the top causes of shipping container failure, stating that this leads to “water ingress, mold, and temperature fluctuations.”13 Repair manuals also emphasize the inspection and replacement of these gaskets. The takeaway here is that despite the seemingly most important massive steel structure, it is often this small, fragile rubber component that determines the fate of millions of dollars worth of cargo. This highlights a critical vulnerability in the system design, where a low-cost part has high-consequence failure modes.
Chapter 2: The Global Market — A Game of Giants
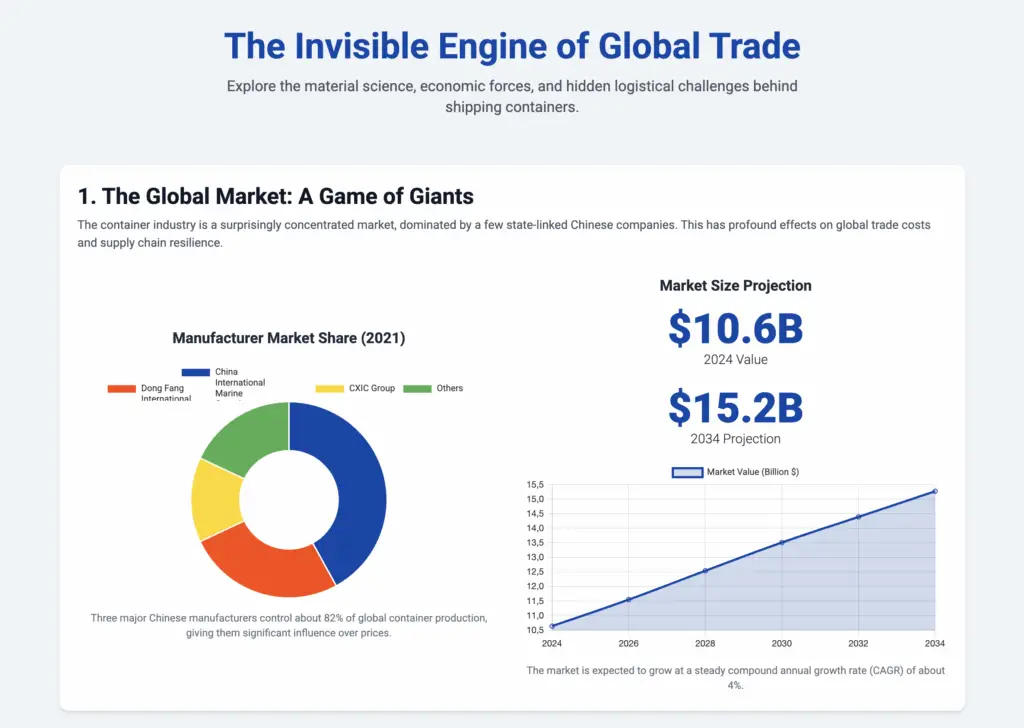
This chapter examines the powerful economic forces shaping the shipping container industry, revealing a highly concentrated market with significant geopolitical and logistical consequences. This data is ideal for market share pie charts, market value bar graphs, and maps showing global production and trade flow dominance.
2.1 Market Size and Growth Trajectory
The global shipping container market is a massive industry, valued at approximately US10.5−10.64billionin2023−2024.ProjectionsestimateitwillreachapproximatelyUS15-15.27 billion by 2033/2034, with a compound annual growth rate (CAGR) of about 3.5% to 4.8%.
The market is dominated by dry storage containers, which hold the largest share. In terms of size, 20′ and 40′ shipping containers are the most common, with 40′ shipping containers holding the highest market share. By floor type, traditional wood floors have the largest share, while bamboo is a rapidly growing segment.
Regionally, the Asia-Pacific region is the undisputed leader, accounting for roughly 50% of the market in 2024 and being the largest producer. China, South Korea, and Japan are the top three shipbuilding countries associated with shipping container demand. Europe, however, is the fastest-growing market.
2.2 Chinese Hegemony: A State-Controlled Monopoly
China’s dominance in container manufacturing is absolute. The country produces an estimated 85% to over 96% of the world’s dry cargo containers and 100% of the refrigerated (reefer) containers.
This market is further concentrated among three key state-linked Chinese companies :
- China International Marine Containers (CIMC): The world’s largest manufacturer, with a market share of approximately 42%.
- Dong Fang International Containers (DFIC): The second largest, with a market share of approximately 26%.
- CXIC Group Containers Co., Ltd.: The third-largest player, with a market share of approximately 14%.
These three companies controlled approximately 82% of global production in the first quarter of 2021. Other sources suggest that CIMC, Singamas, and CXIC control about 90%. This level of concentration is a critical feature of the market.
Table 1: Comparative Analysis of Leading Container Manufacturers
Company | Headquarters | Estimated Market Share (%) | Annual Production Capacity (TEU) | Key Specializations | Notable Corporate Actions |
CIMC | Shenzhen, China | ~42% | 2,000,000 | Dry, Reefer, Special, Modular Homes | Acquired Maersk’s reefer container division |
DFIC | Shanghai, China | ~26% | 1,800,000 | Dry Cargo, Reefer | – |
CXIC Group | Jiangsu, China | ~14% | 900,000 | Dry Cargo, Special, Tank Containers | – |
Maersk Container Industry | Denmark | Not specified | Not specified | Reefer | Reefer division sold to CIMC |
Singamas | Shanghai, China | Not specified | 900,000 | Dry Cargo, Reefer, Special | Supplied energy storage containers |
China’s dominance is not just a result of low-cost labor; it is a strategic control over a critical piece of global infrastructure. These state-linked companies are reported to manage production to strategically keep shipping container prices high, rather than maximizing output, meaning they effectively control a key cost component of global trade. Concerns from the U.S. Federal Maritime Commission that this equipment is “controlled by a state-owned enterprise” and whether “a potential monopoly is manipulating the market” confirm this situation. This combines market share data with geopolitical strategy. The issue is not just that China
makes the boxes, but that it controls the tap. This has profound implications for global inflation, supply chain resilience, and trade policy; all are affected by the production decisions of a handful of state-linked firms in a single country.
2.3 The Leasing Landscape: The Power of Flexibility
The shipping container leasing market is a critical sub-sector, valued at over US$15.8 billion in 2023. It is dominated by major players like Triton International, Textainer Group, Seaco, and CAI International.
Leasing provides shipping lines with significant operational and financial flexibility. It allows them to scale their container fleets up or down in response to demand fluctuations without the massive capital expenditure of purchasing shipping containers outright. Various leasing models are available:
- Long-Term Lease: Offers a stable supply for predictable routes.
- Master Lease: Provides maximum flexibility for managing fleets across many locations.
- One-Way Lease: Allows a shipping container to be dropped off at a different location from where it was picked up, a key tool in combating empty shipping container repositioning costs.
The container manufacturing and leasing industries are deeply intertwined. Leasing companies are the largest buyers of new shipping containers from Chinese manufacturers, acting as the primary customers and financial intermediaries that keep the entire system functioning. Shipping lines need flexibility and want to minimize their capital assets. Leasing companies provide this flexibility by owning the containers and leasing them out. To do this, leasing companies must purchase a large number of new shipping containers. Their primary suppliers are the Chinese manufacturing giants (CIMC, DFIC, etc.). Therefore, the business model of the “Big Three” manufacturers is critically dependent on the financial health and purchasing strategies of the large leasing firms. A drop in leasing demand would have an immediate and severe impact on manufacturing orders. This creates a highly concentrated and interdependent financial ecosystem at the heart of global logistics.
Chapter 3: The Operational Lifecycle — A Hard Life
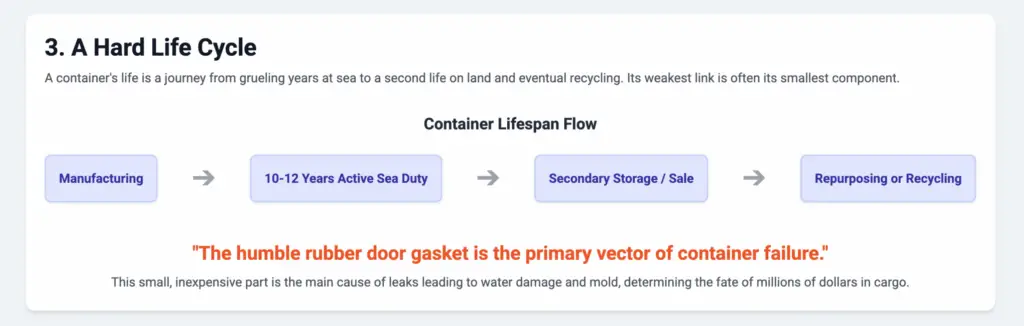
This chapter details the physical realities of a shipping container’s life, its finite lifespan, the damages it incurs, and the processes that keep it in service. This is ideal for creating visuals that show wear and tear, damage hotspots, and repair processes.
3.1 A Finite Lifespan: A 25-Year Journey
A new shipping container typically has a service life of 10-12 years in active sea duty. After retiring from the harsh marine environment, it can endure many more years in secondary storage roles, with a total potential lifespan of up to 25-40 years with proper maintenance.
The key factors that shorten its life are:
- Corrosion (Rust): Described as the “only natural enemy” of steel. Exposure to saltwater and moisture is the primary cause of degradation. Rust weakens the integrity of the steel, making it brittle and prone to fractures.
- Heavy/Improper Use: Dents from impacts with forklifts or during loading damage the protective paint layer, promoting rust formation. Overloading the roof, in particular, can also cause structural damage.
- Environment: The specific routes a shipping container travels (e.g., North Atlantic versus calmer seas) and the types of cargo it carries significantly affect its wear and tear.
3.2 The Damage Catalog: Anatomy of a Failure
Containers are susceptible to a range of common damages that inspectors look for. These can be systematically categorized:
- Structural Damage: Dents, holes, punctures, and scratches on walls and roofs. Bent roofs and deformed floors due to overloading or improper stacking. Twisted frames or cracked corner castings from unbalanced lifting.
- Corrosion: Surface rust is common and treatable, but deep pitting corrosion can compromise structural strength. Welds, areas around the doors, and the undercarriage are particularly susceptible.
- Component Failure: Malfunctioning doors (jammed or difficult to open) due to warped frames or rusty hinges. Degraded or dislodged rubber door gaskets (seals) leading to leaks.
- Internal Damage: Damaged or rotten wooden floors due to water damage or forklift impact. Mold and bad odors due to moisture ingress (“container rain”) or inadequate ventilation.
The industry uses standardized codes to classify damage to make inspection reports uniform. For example, the code C-RF-D
means a Collision resulted in a Dent on the Right Front panel.
3.3 The Science of Repair and Maintenance: Extending Life
A recurring theme is that proactive maintenance is far more effective than reactive repair.7 Repair techniques and maintenance steps are summarized below.
Repair Techniques:
- Rust and Corrosion: Minor surface rust is removed by sanding, wire brushing, or sandblasting, followed by priming and repainting with marine-grade paint. For severe corrosion or holes, the damaged steel section is cut out and a new steel panel is welded in its place.
- Structural Damage: Minor dents can be left, but severe dents or punctures require patching with new steel.
- Floor: Damaged plywood floorboards can be patched or, more commonly, completely replaced.
- Doors and Gaskets: Worn rubber gaskets are replaced. Rusty hinges are lubricated. Warped doors may require structural realignment or complete replacement.
Proactive Maintenance Checklist:
- Regular Inspections: Visually check for rust, dents, and damage.
- Keep it Clean: Regularly wash off dirt, debris, and corrosive substances.
- Roof Maintenance: Clear standing water, snow, and ice from the roof to prevent buildup and corrosion.
- Lubrication: Keep door hinges and locking mechanisms lubricated.
- Gasket Inspection: Inspect and replace caulk and weather stripping annually.
- Proper Foundation: Place the shipping container on a level, well-drained surface to prevent warping.
Table 2: Common Shipping Container Damages, Causes, and Standard Repair Protocols
Damage Type | Common Causes | Visual/Odor Cue | Standard Repair Protocol | Preventive Measure |
Floor Rot | Leaking door gaskets, cargo spills | Spongy floorboards, musty smell | Remove and replace affected plywood panels, treat steel cross-members for rust | Regular gasket inspection, ensure cargo is dry before loading |
Roof Corrosion | Paint damage, standing water, debris buildup | Rust stains, thinning metal, holes | Sand/blast surface rust, prime and repaint. Weld-patch holes | Regularly clean roof and drain standing water |
Warped Doors | Impact, uneven foundation, frame damage | Doors hard to open/close, gaskets not seating properly | Lubricate hinges, realign frame or replace door if necessary | Keep container on level ground, careful handling |
Gasket Failure | UV exposure, age, physical wear | Cracked, torn, or loose rubber gaskets, moisture inside | Remove old gasket and replace with new | Inspect and clean gaskets annually |
Corner Casting Damage | Improper or unbalanced lifting, impact | Cracks, bends, weld damage | Cut out damaged casting and weld on a new standard-compliant casting | Use proper lifting techniques by certified operators |
Chapter 4: The Hidden World of Container Logistics
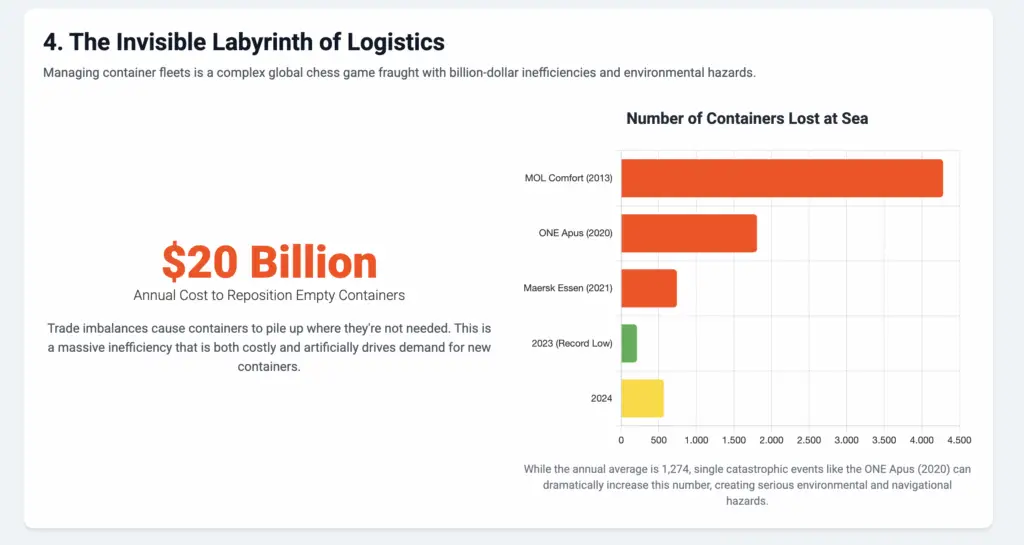
This chapter delves into the complex and often invisible challenges of managing a global fleet of millions of shipping containers. The topics here are well-suited for data visualizations, maps, and process flowcharts that reveal the scale of these problems.
4.1 The $20 Billion Problem: Empty Container Repositioning
The logistics industry spends an estimated $15-20 billion annually to move empty shipping containers from places of surplus to places of deficit. This non-revenue-generating activity can account for up to 8% of a shipping line’s operating costs.
The root cause of this problem is imbalances in global trade. For example, regions like North America and Europe are net importers and accumulate large quantities of empty shipping containers, while manufacturing hubs in Asia face a constant shortage. This is not a simple A-to-B problem; it involves complex forecasting, warehouse storage costs, land transport (truck/train), and sea transport. The cost of moving an empty container is almost the same as a full one because it occupies the same valuable slot on a ship.
Solutions to this problem include:
- Technology: Digital platforms and artificial intelligence help with forecasting and visibility to better match supply and demand.
- Operational Strategies: Promoting “shipping container triangulation” (finding a new outbound cargo near the drop-off point) and “street turns” (the direct transfer of an empty container from an importer to an exporter).
- Leasing Models: One-way leasing shifts the repositioning burden.
- Shipper-Owned Containers (SOCs): Transfers the responsibility to the shipper.
The empty container repositioning problem and the global shipping container shortage are two sides of the same coin. A surplus of idle shipping containers in a European port is useless to an exporter in Shanghai, creating an artificial shortage. This inefficiency in the system, exacerbated by port congestion and other disruptions (like the Red Sea crisis), directly drives up demand for new containers from manufacturers, even though there are millions of available containers worldwide. The shortage is often not an absolute shortage, but a positional one. This means that the inefficiency of the repositioning process directly feeds the profits of the highly concentrated manufacturing sector. The more inefficient the global fleet, the more new boxes need to be built. This is a powerful systemic feedback loop.
4.2 Perils of the Sea: Containers Lost at Sea
An average of 1,274 shipping containers have been lost at sea annually over the last decade. However, this figure fluctuates wildly. In 2024, 576 shipping containers were lost, an increase from the record low of 221 in 2023, but still a small fraction (0.0002%) of the approximately 250 million shipping containers transported annually.
The annual average is heavily skewed by catastrophic events:
- MOL Comfort (2013): Broke in two, losing 4,293 containers.
- ONE Apus (2020): Lost approximately 1,816 containers in a Pacific storm, including 64 with dangerous goods.
- Maersk Essen (2021): Lost approximately 750 containers.
The primary causes are:
- Severe Weather and Rough Seas: The primary factor.
- Parametric Rolling: A dangerous phenomenon where a ship can unexpectedly roll to extreme angles in certain sea conditions, a major area of study for preventing losses.
- Human Factor: Improper stacking, mis-declared shipping container weights, and inadequate lashing.
- Structural Failures: Structural failures of the ship or the shipping containers themselves.
- Geopolitical Factors: The increase in losses in 2024 was partly attributed to ships being re-routed around the Cape of Good Hope to avoid the Red Sea crisis, exposing them to more dangerous waters.
4.3 The Environmental Toll: Sunken Threats
Over 20,000 shipping containers have been lost in the last 15 years. These lost shipping containers pose significant, long-term environmental threats.
Impacts:
- Physical Habitat Destruction: A sunken container can crush sensitive deep-sea ecosystems like coral reefs or seagrass beds. The M/V Med Taipei incident in 2004 resulted in a shipping container being studied on the seafloor of the Monterey Bay National Marine Sanctuary for over 17 years.
- Chemical and Plastic Pollution: Containers can release their cargo, which may include hazardous materials, chemicals, or plastics. The paint on the shipping containers themselves contains toxic anti-fouling compounds like lead and chromates that leach into the water over time. The sinking of the X-Press Pearl off Sri Lanka released billions of plastic pellets and toxic chemicals, creating an “ecological war zone.”
- Navigational Hazard: Partially submerged or floating containers pose a serious collision risk to other vessels, from small yachts to large ships.
4.4 The Dark Side: Illicit Trade and Security
With over 860 million shipping container movements annually and less than 2% being physically inspected, the container system is a primary vector for illicit trade. This includes smuggling drugs, weapons, counterfeit goods, and even human trafficking. Over 300 metric tons of cocaine were seized from ships in 2022 alone.
Security Initiatives:
- UNODC-WCO Container Control Programme (CCP): A joint initiative to build capacity in member countries to improve risk management and target high-risk shipping containers at ports and borders.
- Container Security Initiative (CSI): A U.S. Customs and Border Protection (CBP) program that places officers in foreign ports to pre-screen high-risk shipping containers before they are loaded onto vessels destined for the U.S.
- Smart Containers and SSDs: The use of Smart Security Devices (SSDs) with GPS and door sensors is a key technological solution that allows for real-time tracking, geofencing, and tamper alerts, which can be shared with customs authorities to improve risk assessment.
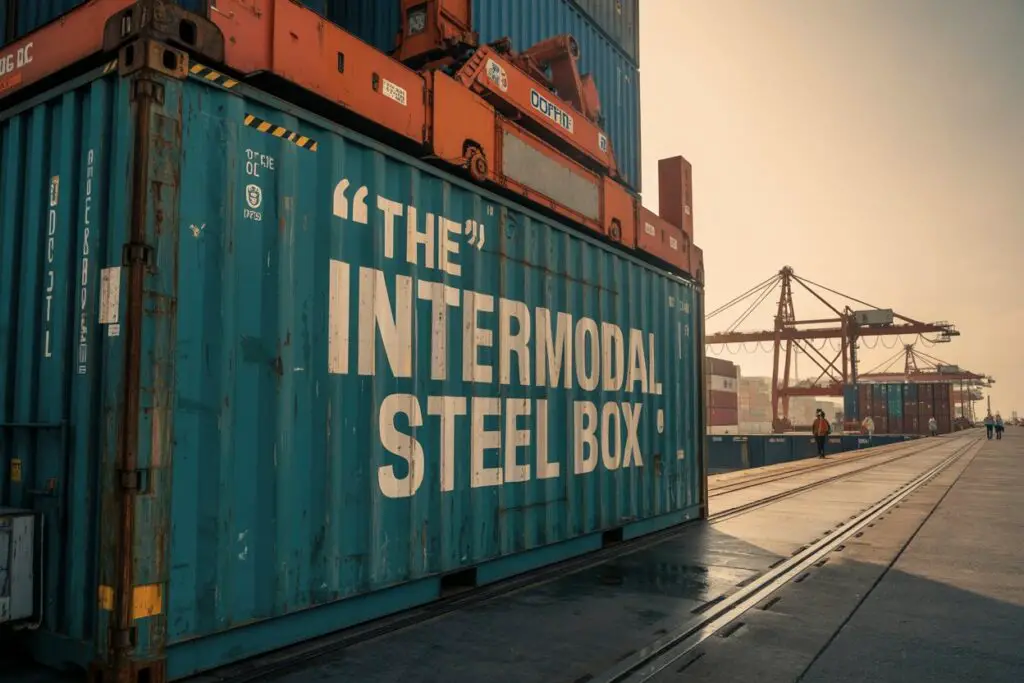
Chapter 5: The Rules of the Game — The World of Standards
This chapter provides a technical breakdown of the international standards that make the entire shipping container system possible. It is designed for readers who need to understand the regulatory and engineering backbone of the industry. This content is excellent for creating reference charts and diagrams explaining the meaning of shipping container markings and testing requirements.
5.1 The ISO Framework: The Language of Intermodality
A series of standards from the International Organization for Standardization (ISO) governs shipping container design, ensuring they are interchangeable worldwide.
Key Standards:
- ISO 668: Defines the classification, external/internal dimensions, and weight ratings for Series 1 containers (e.g., 20ft, 40ft, 40ft High Cube).
- ISO 1496-1: Specifies detailed design requirements and, most importantly, testing procedures for general cargo containers.
- ISO 6346: Dictates the universal coding, identification, and marking system. This includes the 4-letter owner code, category identifier (‘U’ for freight containers), 6-digit serial number, and 1-digit check digit.
- ISO 1161: Details the precise specifications for the corner fittings, the cornerstone of the entire system; these parts allow containers to be lifted, stacked, and secured.
- ISO 3874: Outlines the standardized methods for handling and securing shipping containers.
5.2 The Safety Mandate: CSC and IICL
Convention for Safe Containers (CSC): An international convention established by the IMO. Every container used for international transport must have a valid CSC Safety Approval Plate. This plate indicates that the container meets certain safety standards, including structural tests, and lists important data like the next examination date. Inspections are required within 5 years of manufacture and then at least every 30 months.
Institute of International Container Lessors (IICL): A trade association for the shipping container leasing industry. The IICL publishes its own rigorous inspection and repair criteria (e.g., IICL-6).
While CSC is the mandatory minimum safety standard, the IICL standard is often considered a higher-quality, commercial benchmark in the industry. A container repaired to “IICL standards” is perceived to be in generally better condition than one that only meets the minimum CSC requirements. CSC is a government-mandated safety convention. In contrast, IICL is an industry group of lessors who own the assets and have a financial interest in maintaining their value and longevity. The IICL guide provides detailed criteria for determining whether damage requires repair and applies to both in-service and on/off-hire inspections. It aims to consolidate various standards into one comprehensive standard. Therefore, a lessor’s standard (IICL) is driven by asset value protection, while the international convention (CSC) is driven by minimum safety. This makes the IICL standard the de facto “gold standard” for quality and condition in the secondary market; a nuance that is not obvious at first glance.
5.3 Proof of Strength: Structural Test Procedures (ISO 1496-1)
To be certified, a prototype shipping container design must pass a series of rigorous physical tests defined in ISO 1496-1.
Key Tests:
- Test No. 1 – Stacking: This is the most critical test. It verifies the container’s ability to withstand the weight of a full stack of shipping containers on a ship. A force equivalent to a 3-meter stack height (or a specific load, e.g., 1.8g) is applied to the four corner posts for 24 hours. The container must not show any permanent deformation that would compromise its use.
- Test No. 2 & 3 – Lifting: The shipping container is loaded to twice its maximum gross weight and lifted from the top corner fittings, then the bottom corner fittings, to ensure the frame can withstand lifting stresses.
- Test No. 5 & 6 – Wall Strength: Internal forces are applied to the end walls (0.4P, P being payload) and side walls (0.6P) to simulate the pressure of shifting cargo.
- Test No. 7 – Roof Strength: A concentrated load (e.g., 300 kg) is applied to the roof to ensure it can support the weight of workers.
- Test No. 8 – Floor Strength: Tests the floor’s ability to withstand the heavy loads of a forklift during loading and unloading.
- Test No. 9 & 10 – Racking (Rigidity): These tests measure the shipping container’s resistance to lateral distortion. In the Transverse Racking test, lateral forces are applied to the top corners to simulate forces experienced on a ship. In the Longitudinal Racking test, forces are applied to the base. The container must not deform beyond specified limits.
Chapter 6: Second Life and Beyond
This chapter follows the container after its primary shipping life, exploring its end-of-life options. This is ideal for flowcharts of the end-of-life process and visual galleries of repurposed container projects.
6.1 End-of-Life Pathways: Retire, Recycle, Repurpose
After 10-15 years of sea service, containers are usually retired and sold on the secondary market.26 The main pathways are:
- Refurbishment for Secondary Use: The most common path. Containers are sold for on-land storage for goods, construction materials, or office supplies.
- Repurposing (Cargotecture): A growing trend where shipping containers are used as the primary structural element for buildings.
- Recycling: Containers that are too damaged for reuse are sold as scrap metal.
6.2 The Recycling Process: From Box to Billet
The recycling process is straightforward but requires specialized equipment. Up to 95% of a standard shipping container, especially its steel, is recyclable.
Process Steps:
- Assessment and Pickup: The container’s condition and accessibility are assessed. If it meets certain criteria (e.g., in Northern California), disposal may even be free.
- Dismantling: The container is transported to a processing facility where it is dismantled.
- Material Separation: The different materials are separated: the steel frame and panels, the chemically treated wood floor, the rubber door gaskets, and any other fittings from modifications.
- Processing: The steel is crushed, shredded, melted down, and turned into other metallic products, returning to the manufacturing cycle. The wood and other materials are disposed of according to regulations.
6.3 Cargotecture: The Rise of Repurposed Design
Also known as “arkitainer,” this architectural movement uses shipping containers as the main structural element.83 It has become popular for everything from single-family homes and pop-up shops to large apartment complexes, hotels, and even stadiums (e.g., Stadium 974 in Qatar).
Design Philosophy: The movement is driven by several key principles:
- Sustainability: Reusing a used container saves thousands of kilograms of steel and reduces the need for traditional materials like bricks and cement.
- Modularity: The standardized dimensions of containers make them excellent modular building blocks that can be stacked and combined in creative ways. This also allows for fast, off-site prefabrication and rapid on-site assembly.
- Durability: The inherent strength of the Corten steel structure creates a robust and weather-resistant building frame.
- Aesthetics: A celebration of the industrial, minimalist look.
Practical Challenges: As noted in Chapter 1.3.1, the need to remove toxic floors, add significant insulation (steel is a poor insulator), and make complex modifications can, contrary to popular belief, sometimes make container homes more expensive than traditional construction.
Chapter 7: The Future of the Box — Smart, Autonomous, and Adaptable

This final chapter offers a forward-looking perspective on the technological innovations poised to redefine the shipping container and the logistics industry. This section is ideal for conceptual diagrams and futuristic visuals.
7.1 The Smart Container Revolution: From “Dumb Box” to Connected Asset
The core concept is to make a standard container “smart” by equipping it with self-powered IoT gateway devices and sensors. This transforms it from a passive box into an active, data-generating node in the supply chain.
Sensors collect data and transmit it via multiple communication protocols, such as cellular or satellite, to a cloud-based platform. Stakeholders access this data through web applications or APIs, enabling real-time monitoring and process automation.
Table 3: Data Points Collected by Smart Container Sensors
Sensor Type | Data Collected | Key Use Case/Benefit |
GPS | Real-time location, geofencing, route deviation alerts | Theft prevention, accurate ETA |
Temperature/Humidity | Monitors internal environment | Protects perishable/sensitive cargo (food, pharma) |
Shock/Vibration | Detects impacts and rough handling | Damage detection, liability assignment |
Door Sensor (Light/Magnetic) | Detects unauthorized door openings | Security, theft detection |
Atmospheric (CO2) | Can detect illicit cargo like human or wildlife trafficking by monitoring CO2 levels | Illicit cargo detection |
The benefits of smart containers include increased visibility, improved cargo security, reduced spoilage, cost savings, predictive maintenance, and more efficient customs processing.
7.2 The Promise of Autonomous Shipping: The Uncrewed Vessel
Maritime Autonomous Surface Ships (MASS) are vessels that can operate with little or no human interaction, using artificial intelligence, advanced sensors (radar, lidar, cameras), and satellite communication.
The IMO’s levels of autonomy are:
- Degree One: Decision support for the crew on board.
- Degree Two: Remote control with crew on board.
- Degree Three: Remote control without crew on board.
- Degree Four: Fully autonomous ship that makes its own decisions.
Autonomous ships promise greater efficiency (24/7 operation), increased safety (eliminating human error, which causes >75% of incidents), and optimized fuel consumption through AI-powered route planning. This will fundamentally change container logistics, providing more predictable and continuous flows. However, challenges remain, such as high capital costs, cybersecurity threats, regulatory hurdles, and the need for highly reliable onboard systems (e.g., redundant engines) to replace human maintenance crews.
7.3 Conceptual Designs: Foldable and Modular Containers
As a direct response to the multi-billion dollar empty repositioning problem, foldable or collapsible containers are designed to be collapsed when empty.
The key benefit is that multiple collapsed containers (e.g., 4 or 5) can be stacked and shipped in the space of a single standard container. This significantly reduces transportation and storage costs for empty units. They are often made from lightweight, durable, and recyclable materials. Designs vary, but the goal is to reduce the container’s volume by up to 75% when empty.
Although foldable containers offer an attractive solution to the repositioning problem, their adoption faces significant hurdles related to cost, durability, and operational complexity. They are more expensive to manufacture, have more moving parts that can fail, and may have lower stacking capacity and lifespan than their traditional, rigid counterparts. A foldable structure is inherently more complex than a simple welded box; it will have hinges, locks, and seams. This complexity increases the manufacturing cost. It also introduces more potential failure points (rust at hinges, gasket failures) that could reduce overall structural integrity, especially the critical racking and stacking strength (a potential conflict with ISO 1496-1 test requirements). There is also an operational cost in the time and labor required to fold and unfold containers in depots. Therefore, the total cost of ownership of a foldable container is a complex equation that balances the savings in repositioning against higher initial capital costs, potentially higher maintenance costs, and operational complexities. This explains why they have not yet been widely adopted despite their obvious benefits.
Conclusion: The Enduring Legacy and Future Evolution of the Steel Box
The findings of this report reaffirm that the genius of the shipping container lies in its standardization, which has enabled global efficiencies but also created systemic concentrations and vulnerabilities. The container is not just a commodity transport vehicle, but a platform that has reconfigured global trade itself. Looking forward, the next evolution of the container – smart, adaptive, and integrated into autonomous systems – is poised to trigger a new wave of transformation in global trade, with a shift in focus from physical efficiency to data-driven, intelligent logistics. This evolution promises to make supply chains more transparent, secure, and efficient, while also bringing new challenges such as cybersecurity, data privacy, and the impact of automation on the workforce. The legacy of the steel box is enduring, and its future will continue to be shaped by the possibilities offered by digitalization.
Appendix
Table A1: Technical Specifications of Standard ISO Containers (20ft, 40ft, 40ft HC)
Feature | 1C (20ft Standard) | 1A (40ft Standard) | 1AAA (40ft High Cube) |
External Length | 6.058 m (19′ 10.5″) | 12.192 m (40′ 0″) | 12.192 m (40′ 0″) |
External Width | 2.438 m (8′ 0″) | 2.438 m (8′ 0″) | 2.438 m (8′ 0″) |
External Height | 2.591 m (8′ 6″) | 2.591 m (8′ 6″) | 2.896 m (9′ 6″) |
Minimum Internal Length | 5.867 m (19′ 3″) | 11.998 m (39′ 4.375″) | 11.998 m (39′ 4.375″) |
Minimum Internal Width | 2.330 m (7′ 7.73″) | 2.330 m (7′ 7.73″) | 2.330 m (7′ 7.73″) |
Minimum Internal Height | 2.350 m (7′ 8.5″) | 2.350 m (7′ 8.5″) | 2.655 m (8′ 8.5″) |
Maximum Gross Mass | 36,000 kg (79,370 lbs) | 36,000 kg (79,370 lbs) | 36,000 kg (79,370 lbs) |
Tare Weight (Typical) | ~2,200 kg (4,850 lbs) | ~3,750 kg (8,270 lbs) | ~3,900 kg (8,600 lbs) |
Payload Capacity (Typical) | ~33,800 kg (74,520 lbs) | ~32,250 kg (71,100 lbs) | ~32,100 kg (70,770 lbs) |
Cubic Capacity | ~33.2 m³ (1,172 ft³) | ~67.7 m³ (2,390 ft³) | ~76.4 m³ (2,700 ft³) |
Table A2: Glossary of Key Terminology
Term | Definition |
TEU | Twenty-foot Equivalent Unit. A standard unit of measurement used in the logistics industry to define cargo capacity. A 20ft container is equal to 1 TEU. |
Corten Steel | A weathering steel alloy that exhibits high resistance to atmospheric corrosion. Commonly used in container construction. |
CSC | Convention for Safe Containers. An IMO convention that sets international standards for the structural safety and inspection of containers. |
IICL | Institute of International Container Lessors. A trade association for the container leasing industry that sets standards for inspection and repair. |
Racking | A structural test that measures a container’s resistance to lateral distortion, especially during movements on a ship. |
Parametric Rolling | An event where a ship rolls to unexpectedly and dangerously large angles in certain wave conditions. A significant cause of container losses. |
Cargotecture | An architectural style that uses shipping containers as the main structural element. A portmanteau of “cargo” and “architecture.” |
WWT | Wind and Watertight. A condition indicating that a container is sealed to protect cargo from the elements. |
Table A3: Major Container Manufacturers and Leasing Companies
Category | Company Name |
Manufacturers | China International Marine Containers (CIMC) |
Dong Fang International Containers (DFIC) | |
CXIC Group Containers Co., Ltd. | |
Singamas Container Holdings Ltd. | |
Maersk Container Industry AS (Reefer division acquired by CIMC) | |
Sea Box Inc. | |
W&K Container | |
Leasing Companies | Triton International |
Textainer Group Holdings | |
Seaco Global Ltd. | |
CAI International, Inc. | |
Florens Container Services (owned by COSCO) | |
Beacon Intermodal Leasing, LLC | |
Touax Group | |
SeaCube Container Leasing Ltd. | |
CARU Containers B.V. |