Hi everybody ?
We continue to discover for you. Our container house on today’s tour is from USA.
Today we are featuring another stunning container residence that is making its rounds on social media.
Said to have taken about 18 month (lots of welding and fabrication) to complete, The Cascadia Container Residence definitely worth checking out. Comprising of 3 bedrooms and 2.5 baths, this container has 1600 sq. ft. of living space and 320 sq. ft. of covered 2nd floor deck space. This container home also has:
- Heated, polished concrete floors on the entire bottom floor
- Heated tile floors on the entire 2nd floor
- Central air and fire place
- Spray foam insulation to keep it cozy in the cold winter’s where it gets well below 0 in the winter
- A 22′ sliding barn door made of recycled container pieces so the entire home can be closed up with steel doors
The Cascadia Container Residence was made with 6 containers in Leavenworth, Washington. This distinctive second home is custom-made for Greg and Rania, the home owner’s, family vacations. And the exterior finish? No board and batten or cedar shingles to disguise this honest bunch of boxes: the shipping containers, with their distinctive hinges, corrugation, bolts and rods will all be industrial dark green, with some accent trim. Just paint.
Living in a Container explores projects made with shipping containers around the world and shares them for you.
Don’t forget to take a look at the structures made with other amazing shipping containers on our site!
We invite you to send in your story and container homes photos too so we can re-share and inspire others towards a simple life too. Thank you!
You can share this using the link and social media re-share buttons below. Thanks!
» Follow Living in a Container on Social Media for regular shipping container house updates here «
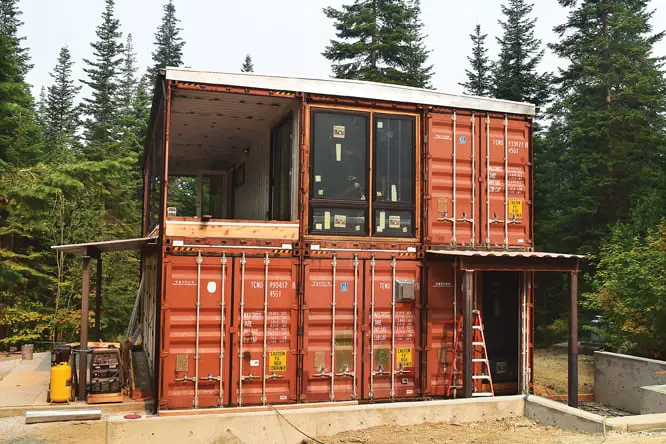
Just a few years ago, the young owners, living in Seattle but with north central Washington roots, were ready for their own ski retreat near Stevens Pass. They were thinking remodeled shed, cabin, tiny house, something small and conventional. They liked the looks of a neighbor’s place, they contacted the architect, he liked a certain builder… and they were pleased that Syndicate Smith (architect Todd Smith of Leavenworth) and One-way Construction together had this relatively new budget-conscious idea they wanted to try.
By the summer of 2016 the owners had eagerly embraced the concept of a container cabin; Greg is in the maritime industry, so he was familiar with the ubiquitous 8’x20’ shipping containers, at least theoretically. Then they expanded the idea, and the little house on its timbered 2.5-acre lot near Lake Wenatchee grew into a more luxurious six-box structure.
In September of 2016, the eight 8’x20’ containers — two are for outbuildings — purchased from Northwest Container Services, were one-by-one trucked over Stevens Pass to a staging area at a nearby highway rest stop. From there they were moved to various spots on the site for preparation (with the neighbor’s approval and undoubted curiosity) and were eventually hefted into position with a boom-crane. Picture six bricks piled into a two-brick high long rectangle. Only bigger, much bigger.
The most grueling part of the process involved metal on metal. State building codes required a state-certified welder for this job, which was deemed industrial rather than residential. Accordingly, One Way’s welder received advanced training and certification in time to do most of the exacting work of connecting the six metal boxes (The other two are for storage adjacent to the garage.) Creating flashing — U-shaped tube steel faux beams to cover the interior seams — forming the patio roof and cutting and placing wood windows and doors into metal openings was relatively easier.
As explained as he showed the seams between units, “These containers are all held together with two-inch-long welds at four-inch intervals.” (For non-builders, that’s a lot of labor and expensive welding compound.)
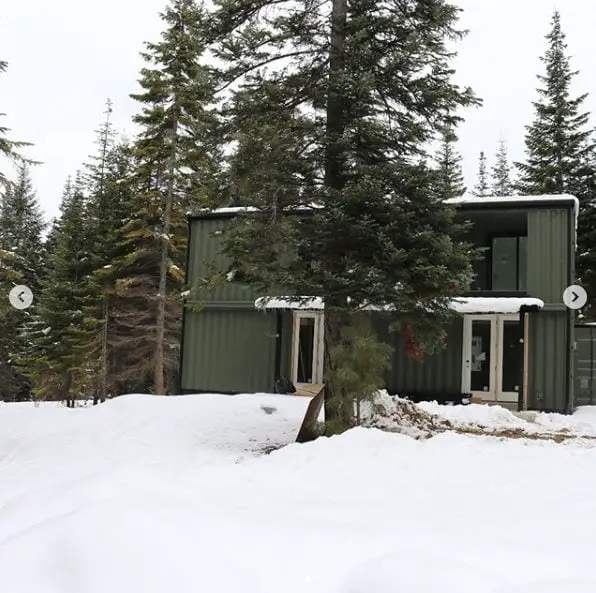

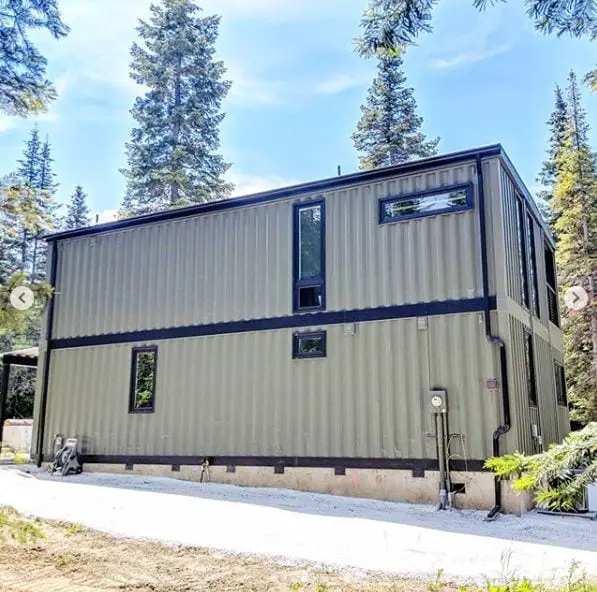
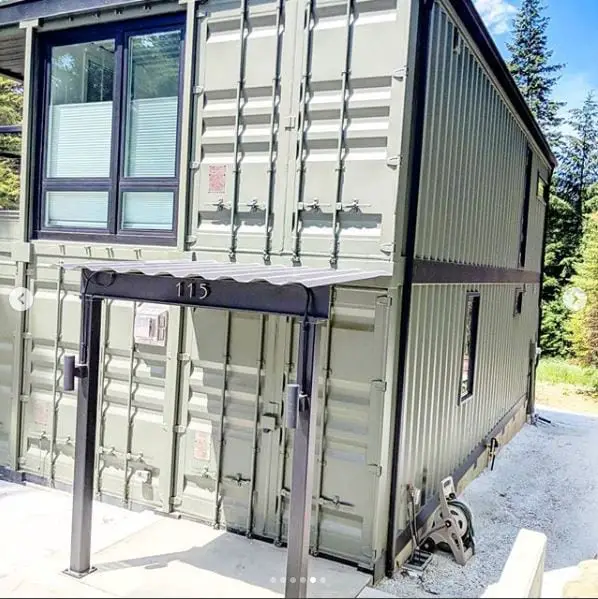
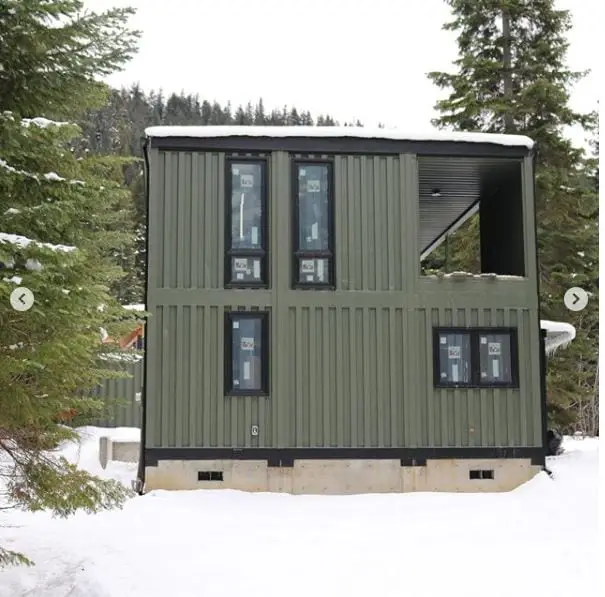
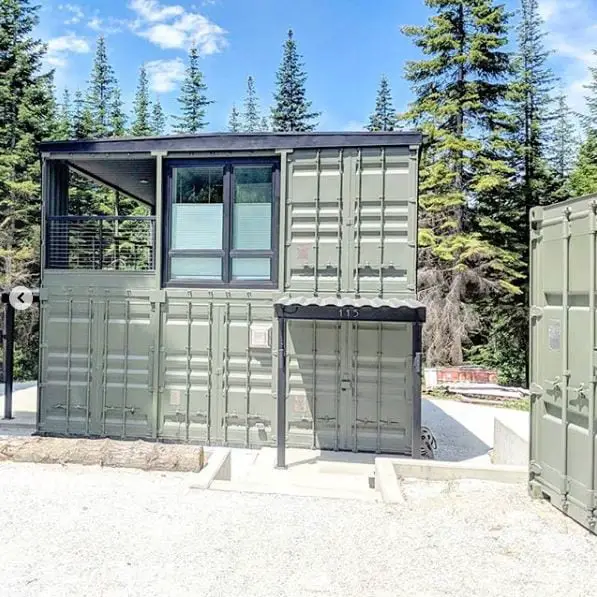
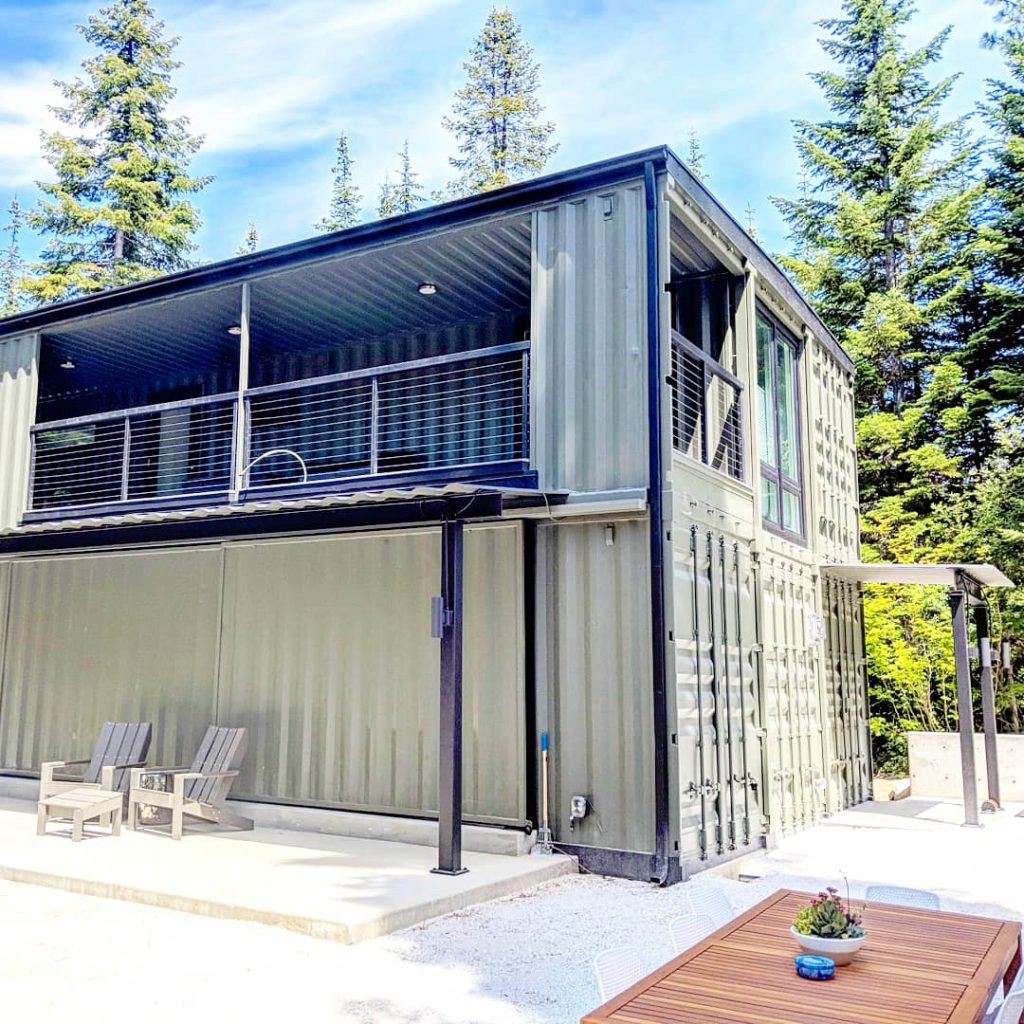
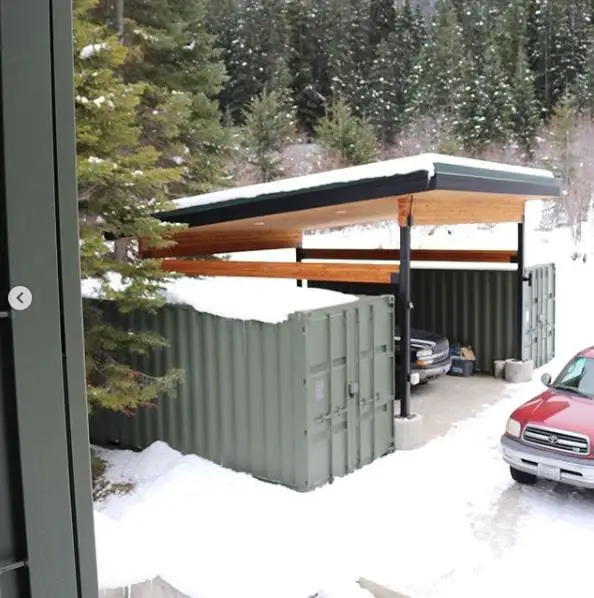
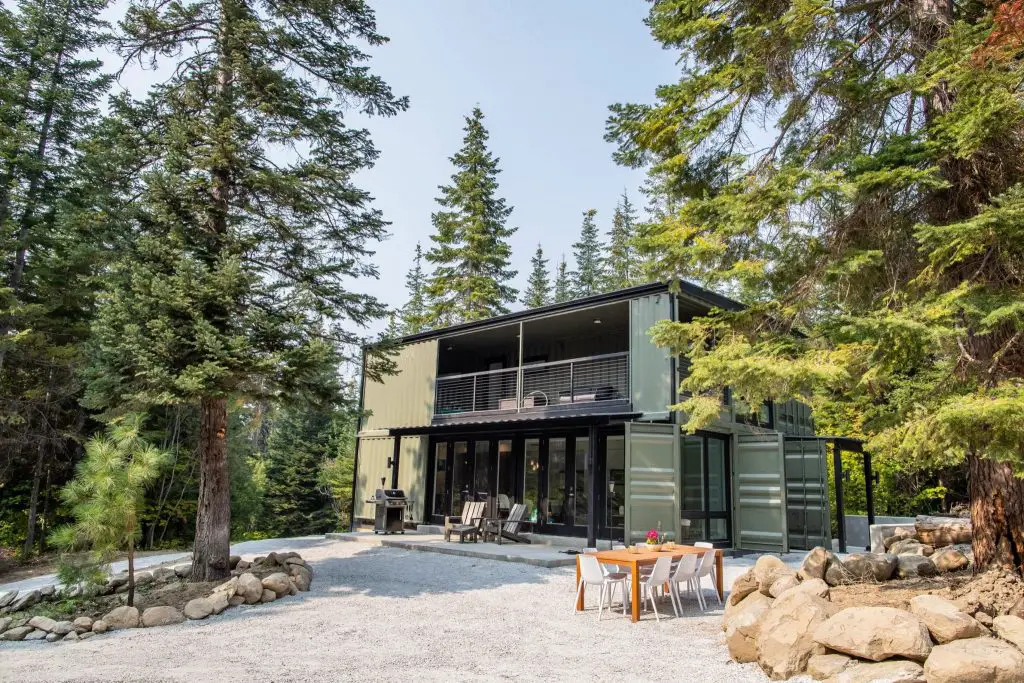
He said the whole crew was very fire-conscious. “All summer long, we had a guy with a water hose just standing on the roof — and his only job was to watch for sparks.”
The long sweep of polished cement flooring in the downstairs living area unites the three spaces for cooking, dining and comfy seating, and the wall of south windows visually adds dimension to its 16’ x20’ footprint. The “high bay” containers offer 9.5-foot ceilings — a real boon to the builders.
A third heating source was added — now there’s hydronic (hot water in pipes) floor heating up and down, a propane stove, and a ducted forced-air system. That and three to five-inches of R-38 insulation — the standard is R-21 — in roof and sides insures winter comfort and walk-away ease.
The original plan for wood flooring in the second story turned into “gypcrete” poured over the floor piping, then completely covered with artisan tilework, and the first-floor concrete patio was extended out from the house for more outdoor living space. Bedroom reading lamps, once sconces, became pendants, with different wiring.
“When you think that the eight boxes, shipped to the site, only cost about $20,000, you can see that a smaller house, especially a single story with standard finishes, could be very cost-effective. This house — exactly what the owners wanted — pencils out to about the same as a stick built house of the same quality, maybe a little more.”
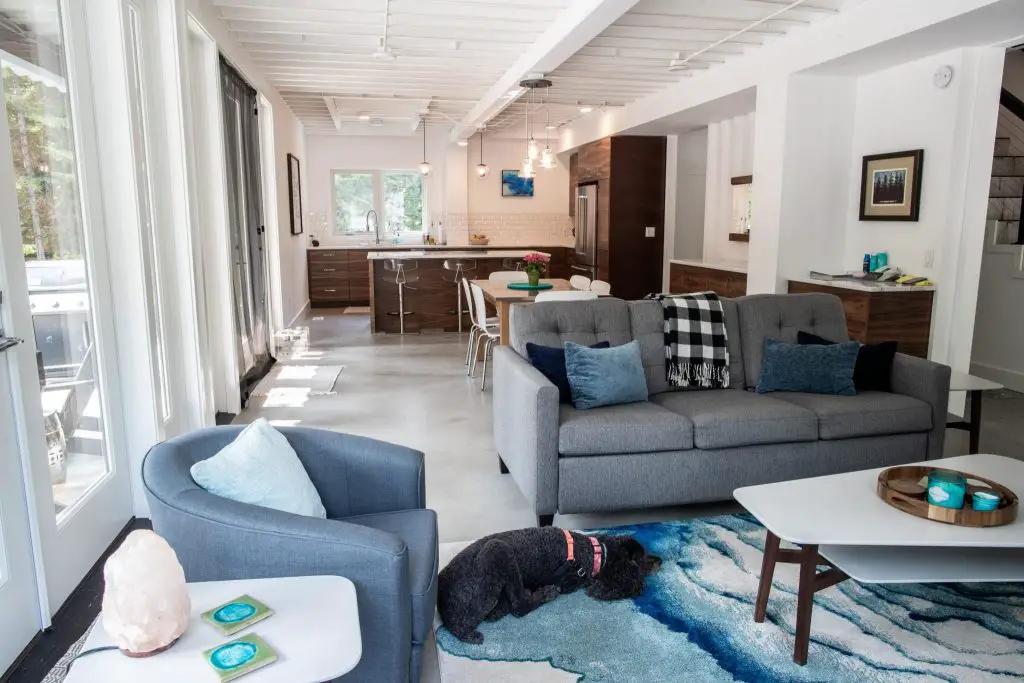
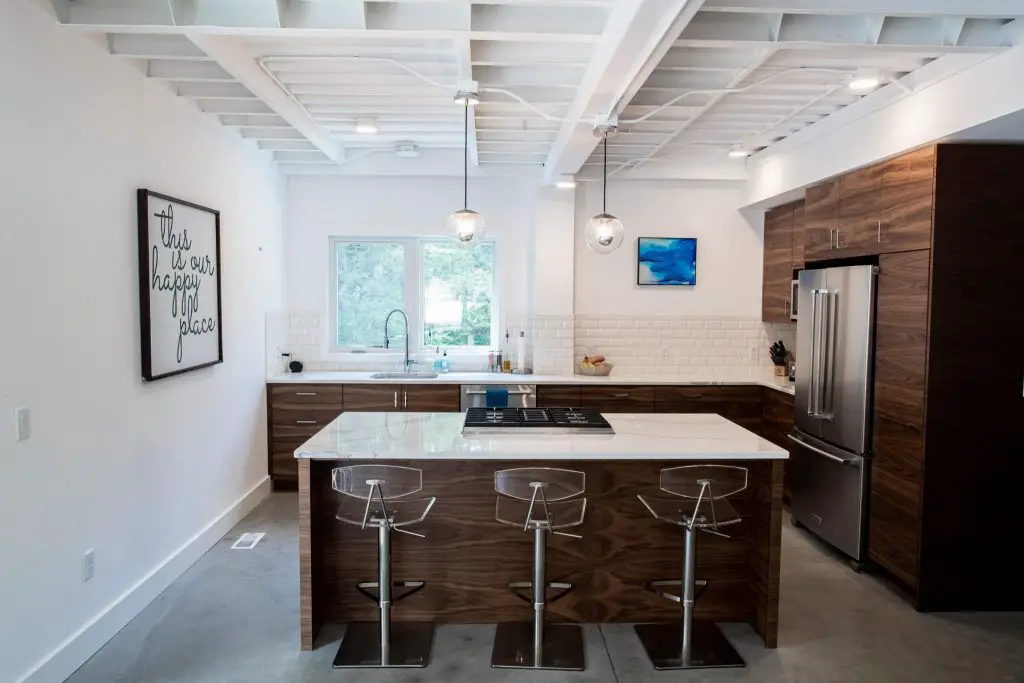
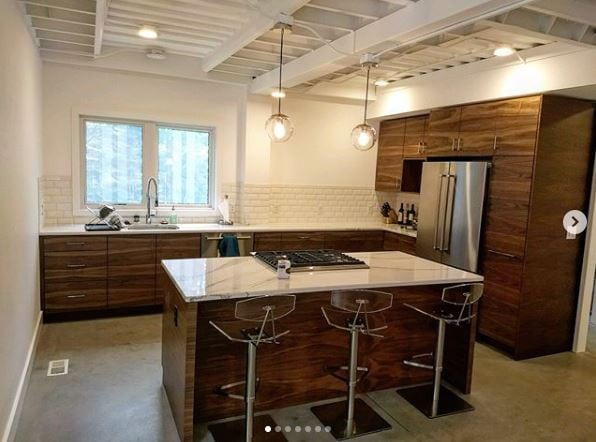
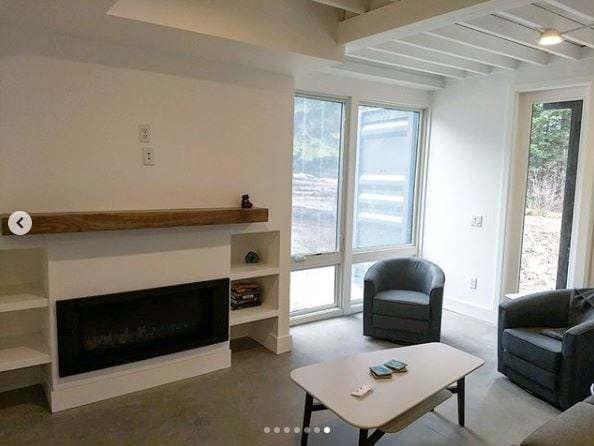
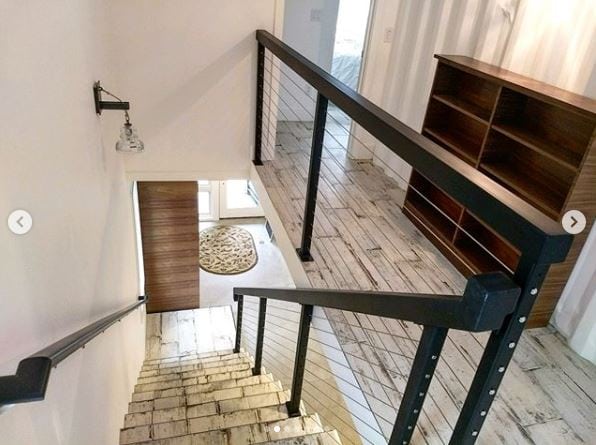
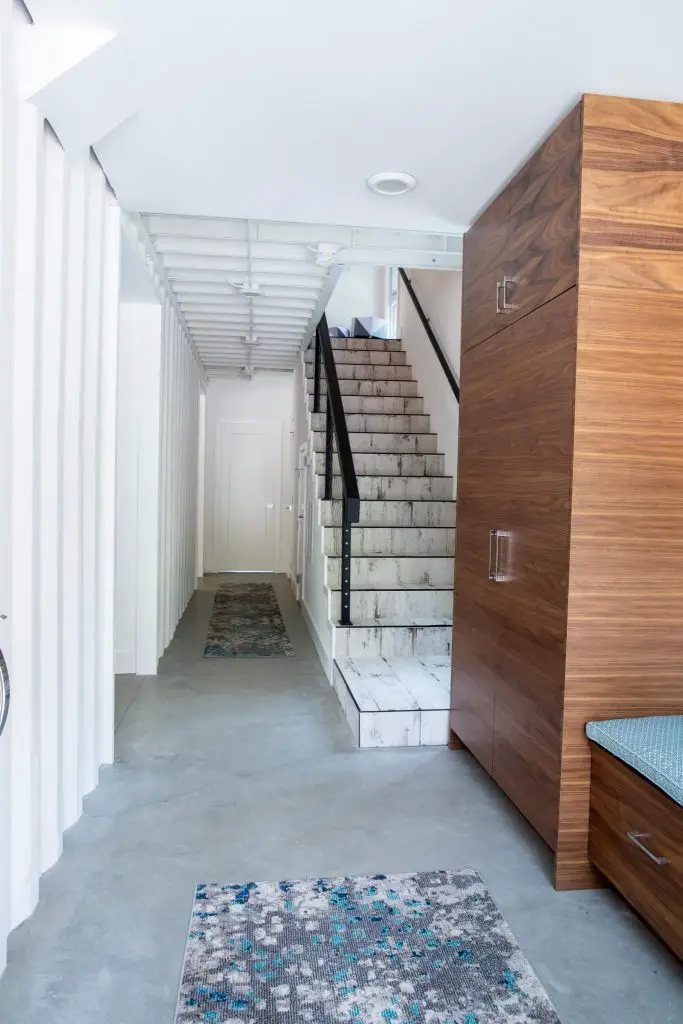
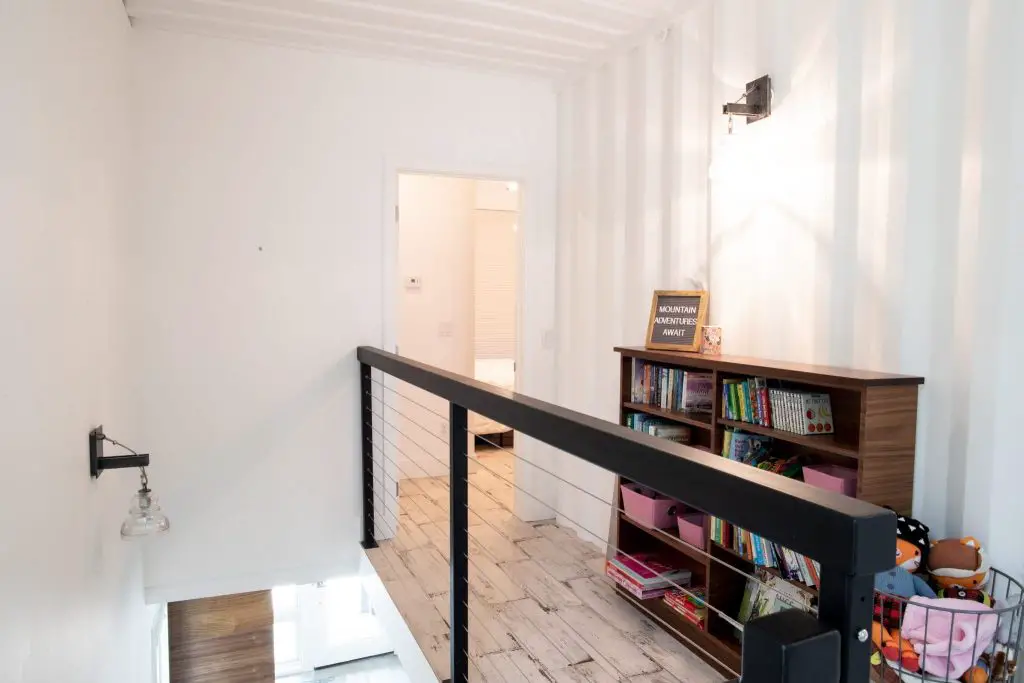
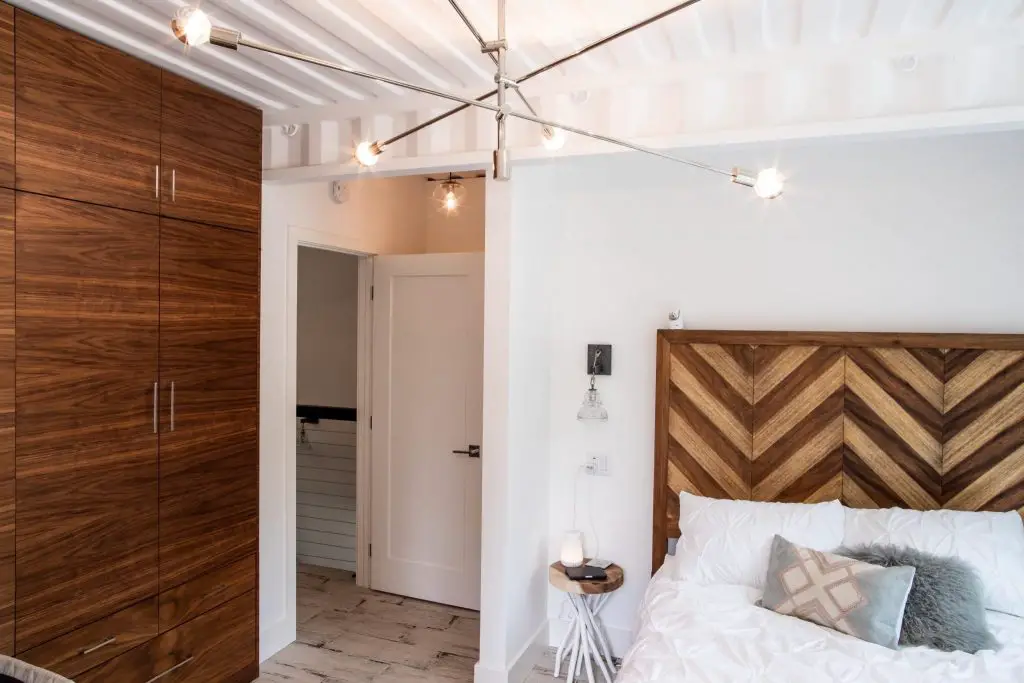
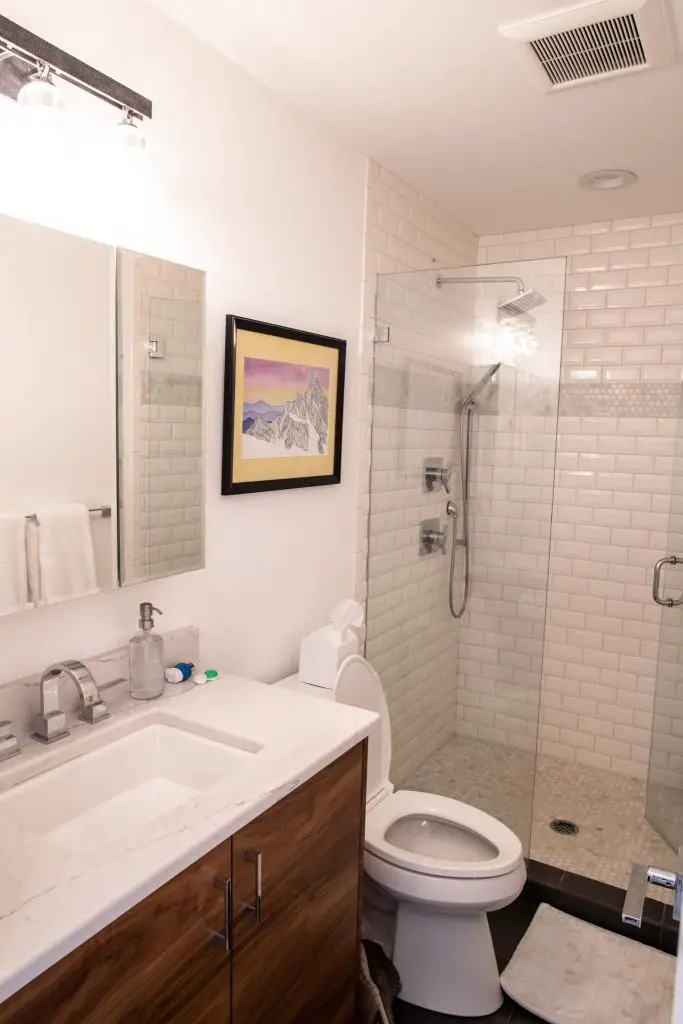
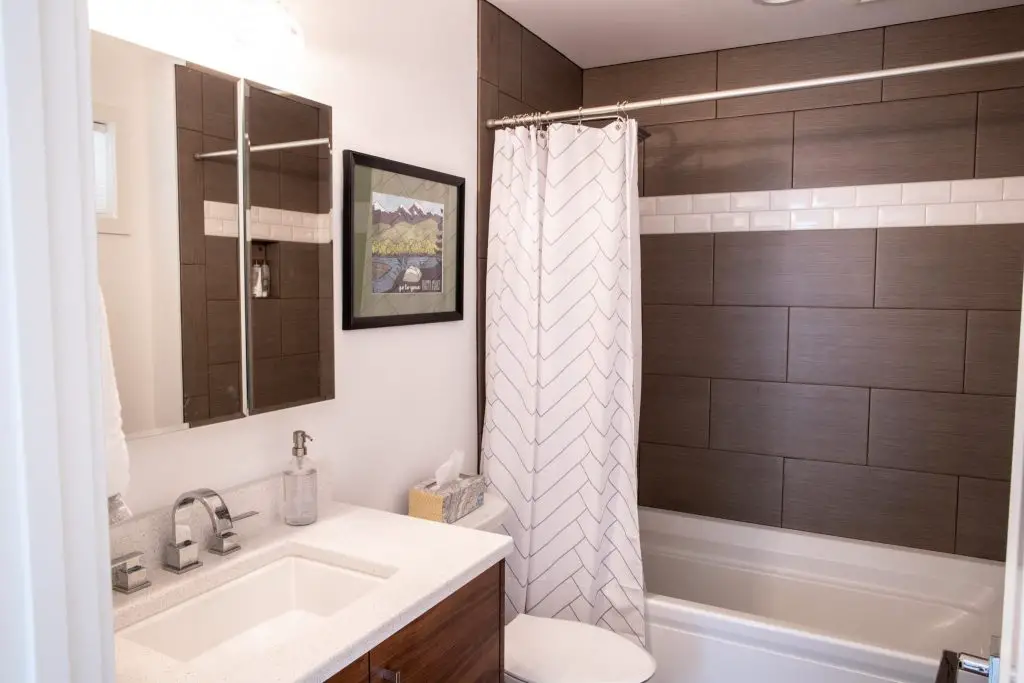
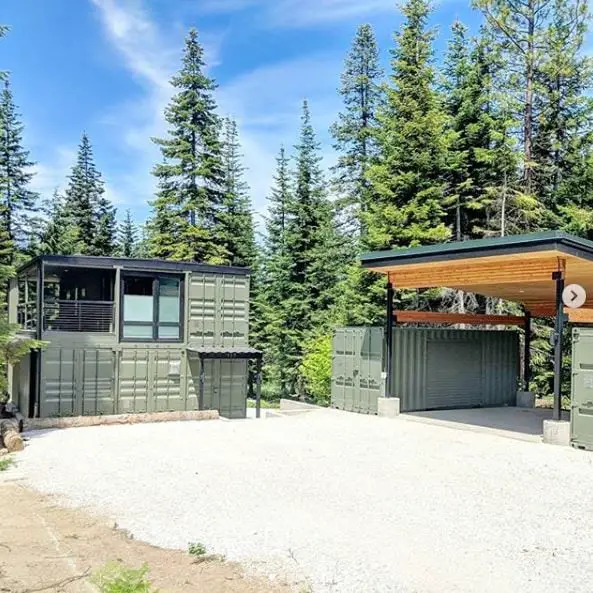
Give this boxy metal house some months for the tree-toned paint to blend it into the lot, and for the inevitable softening of fabric, furnishings and fixtures. Give it a year to settle into the landscape, with native grasses growing to the patio, silent woods surrounding it.
Wow what an interesting story behind this home!
Photo Source: Brandon from One Way Construction, One Way Construction IG, @davidalansorensen, Blogging The Good Life