As the world grows increasingly conscious about sustainable living, shipping container homes have surfaced as a unique and cost-effective housing option. Living innovatively in these repurposed structures is not only about embracing minimalism but ensuring it’s done right, with an understanding of cost implications. Our exploration into the world of shipping container homes will delve into the necessary details, providing you with everything you need to know about their cost. From understanding the basic concept of these homes to implementing real-life case studies for a practical view, we’ll cover it all.
The Basics of Shipping Container Homes
Understanding Shipping Container Homes and Their Costs
Shipping container homes are growing more popular as an efficient, economical, and environmentally sustainable residential option. These structures involve re-purposing industrial shipping containers into complete living spaces. Apart from being a creative solution to housing needs, they are often lauded for their resilience, easy customization, and inexpensive construction costs.
The Basic Process and Costs Associated
The process of converting a shipping container into a livable space involves several steps, each with its own costs. First and foremost, you’ll need to purchase the shipping container itself. Depending on its size and condition, a new container can cost from $3,000 to $5,000, while used ones are available from $1,200.
After securing a container, the next expense is usually customization. This includes installing windows, doors, insulation, plumbing, and electricity. These modifications can add several thousand dollars to the cost. For example, insulation usually costs between $1,000 to $4,000, depending on the material used. The installation of utilities, including water, electricity, and sewerage, can also vary but often comes to around $10,000.
The interior furnishing, fixings, and fittings are additional costs. These expenses can vary widely, depending on your taste and preference. High-end finishes and luxury appliances can push the budget higher, while recycling materials, DIY, or going for minimalistic designs can help minimize costs.
Benefits and Savings
Although the initial setup costs may seem high, the overall long-term maintenance and operational costs of shipping container homes can be much lower than traditional houses. They tend to be more energy-efficient as they are smaller in size, which equates to lower heating and cooling costs. Moreover, due to their durable nature, repair and renovation costs are often less frequent and more affordable compared to standard houses.
Different Types of Shipping Container Homes and Their Costs
There are various types of shipping container homes, and each has a unique cost factor. A single-container home usually costs around $25,000 to $35,000. Double-container homes, offering more space, maybe around $40,000 to $70,000. More expansive homes with multiple containers can cost anywhere from $100,000 and up. The cost ultimately depends on the size, design, and the finishes chosen by the owner.
Unique Features Influencing Pricing
Shipping container homes can include several distinct features which may influence their costs. Some homeowners incorporate solar panels or green roofs for sustainability, which increases the initial expenditure but potentially leads to long-term savings. Others may include high-end glass façades or custom-built storage, which can raise the overall cost. The location and site preparation costs, such as foundation and delivery charges, also play a significant role in estimating the total cost of a shipping container home.
Understanding the costs involved is essential if you’re considering venturing into shipping container homes. However, it’s crucial to remember that their flexibility and sustainability often make the initial investment worth it. With their cost-effectiveness over time, environmental friendliness, versatility, and quick construction time, shipping container homes are becoming a trend in various housing requirements.
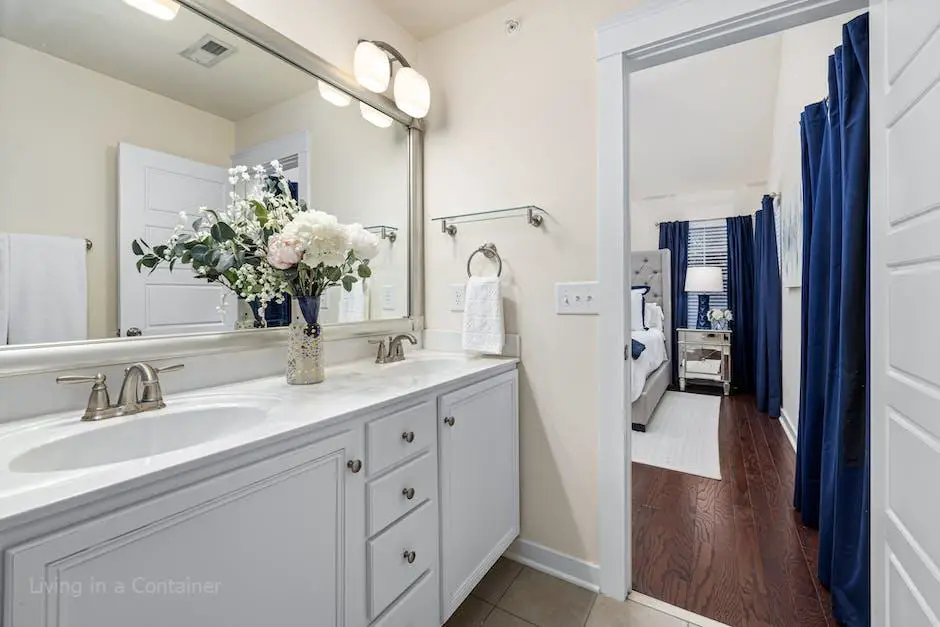
Cost Factors for Shipping Container Homes
Acquisition Cost of a Shipping Container
When determining the potential expense of a shipping container home, the initial cost of procuring the shipping container must be taken into account. Prices can fluctuate, generally beginning around $1,500 for a used container and going up to an estimated $6,000 for a brand-new one. Factors like the size of the container (such as 20ft, 40ft, and so forth), the condition (new or used), and the current marketplace conditions can dramatically sway the beginning purchase price.
Land Requirement
The next factor to consider is the land where the shipping container home will be built. The cost of land varies significantly across different regions in the U.S. According to the U.S. Bureau of Economic Analysis, the average cost of a residential land in 2020 was $5,182 per acre. However, cheaper land may come with increased costs in terms of accessibility to utilities, guaranteeing a level site, and obtaining necessary permissions and permits.
Modification and Construction Costs
Modifying shipping containers to make them livable is a significant cost factor. This includes the cost of cutting and framing openings for doors and windows, strengthening structural integrity, and adding a foundation. Other costs include site preparation, delivery and placement of containers, and labor. Labor costs can vary widely, but construction costs alone could range from $25,000 to over $200,000 depending on the project’s complexity.
Interior Design, Insulation, Plumbing, and Electrical Work
These aspects greatly influence the final cost of your shipping container home. Interior design finishes, such as cabinetry, appliances, and flooring, can range as low as $10,000 to more than $80,000 depending on the materials and finishes chosen. Insulation is another crucial factor, especially since steel is a good conductor of heat. The cost of insulation varies, but it’s important not to skimp on this detail. Plumbing and electrical installation costs also add up, and can vary widely depending on the extent of the project.
Impact of Size, Complexity, and Quality of Fixtures
The larger and more complex your shipping container home, the higher the cost. Adding extra containers, whether for additional space or for creating complex designs, significantly adds to the overall cost. The quality of fixtures, fittings, and finishes you choose can drastically change the final price as well. Luxurious finishes, high-end appliances, and custom fixtures can significantly increase the cost.
When considering the costs associated with owning a shipping container home, a considerable range exists. Prices can extend from a manageable $40,000 to a more extravagant $300,000. Factors that can impact this cost can vary from your chosen finishings and the complexity of your design, to the size of your home and its location— yet, the overall sustainability, durability, and adaptability of these homes make them a viable contender within the housing market.
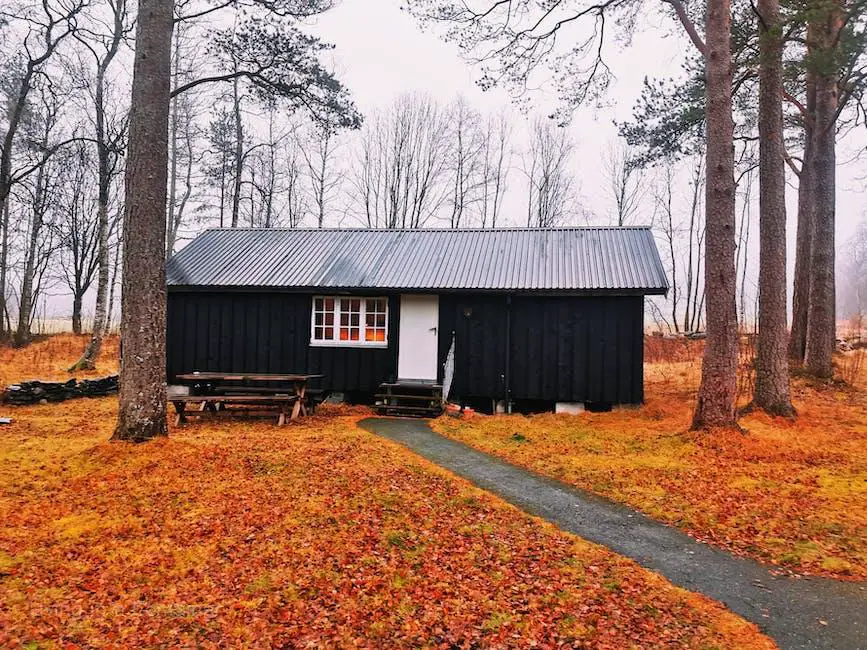
Comparing Costs: Shipping Container Homes Vs Traditional Homes
Economic Comparison: Traditional Homes Versus Shipping Container Homes
The battle of costs between constructing a traditional home or choosing a shipping container home hinges on several variables. Primarily, the size and location of your future home play a substantial role in dictating the total cost. Larger square footage demands more materials and labor for its completion, inescapably leading to higher price points. Similarly, location is a key player in terms of fluctuating property values, contrasting local building codes, and disparities in labor and material costs.
If we zoom in on the costs surrounding a traditional home build – it’s usually somewhere between $150 and $400 per square foot. This is dependent on the location’s property value, the size of the home, and the specificity of the design. By aggregating costs like permits and inspections, site preparations, foundational work, and the physical construction, a regular 2,600 square foot home will typically relegate homeowners between $240,000 and $710,000.
Shipping Container Homes Cost Breakdown
On the other hand, the cost to build a shipping container home can be significantly cheaper. The raw container itself costs between $1,400 to $4,500 per unit. You’d typically need two to three containers for an average-sized home. That puts material cost roughly between $3,000 and $13,500. But that’s just the start.
Site preparation, delivery, and placement of the containers can vary widely but usually run between $1,000 and $5,000. Then comes modification costs, including cutting windows and doors, insulating, and addressing any structural compromises. Thes costs typically range from $1,000 to $6,000 per container.
Wiring and infrastructure set up typically costs between $50 and $200 per hour for a professional installer, not factoring in the price of materials. Then there’s interior finishing, including plumbing, kitchen and bathroom fixtures, flooring, and painting. These costs can also vary substantially depending on the level of luxury you’re pursuing but generally run between $20,000 and $30,000.
All told, the total cost for a shipping container house can range from $25,000 to $40,000 for a bare-bones model, to $75,000 to $150,000+ for an excellent, high-end home.
Bearing in Mind Labor Costs and Duration
It’s important to bear in mind that while building homes with shipping containers can often be more cost-effective compared to traditional houses, they frequently require specialized labor. This is principally because a unique set of skills and knowledge is required to modify and successfully assemble the containers. In locations where there is scarcity of such skilled personnel, costs might inevitably climb.
On a positive note, construction using shipping containers can often be done more swiftly. Where conventional homes can take anywhere from half a year to a full year to build, shipping container homes can be finalized in a few weeks or months. This, of course, is subject to factors such as complexity and size of the build as well as how much the containers have been pre-fabricated prior to arriving on site. This quicker turnaround could translate to financial savings, assuming that the build proceeds without any major hitches.
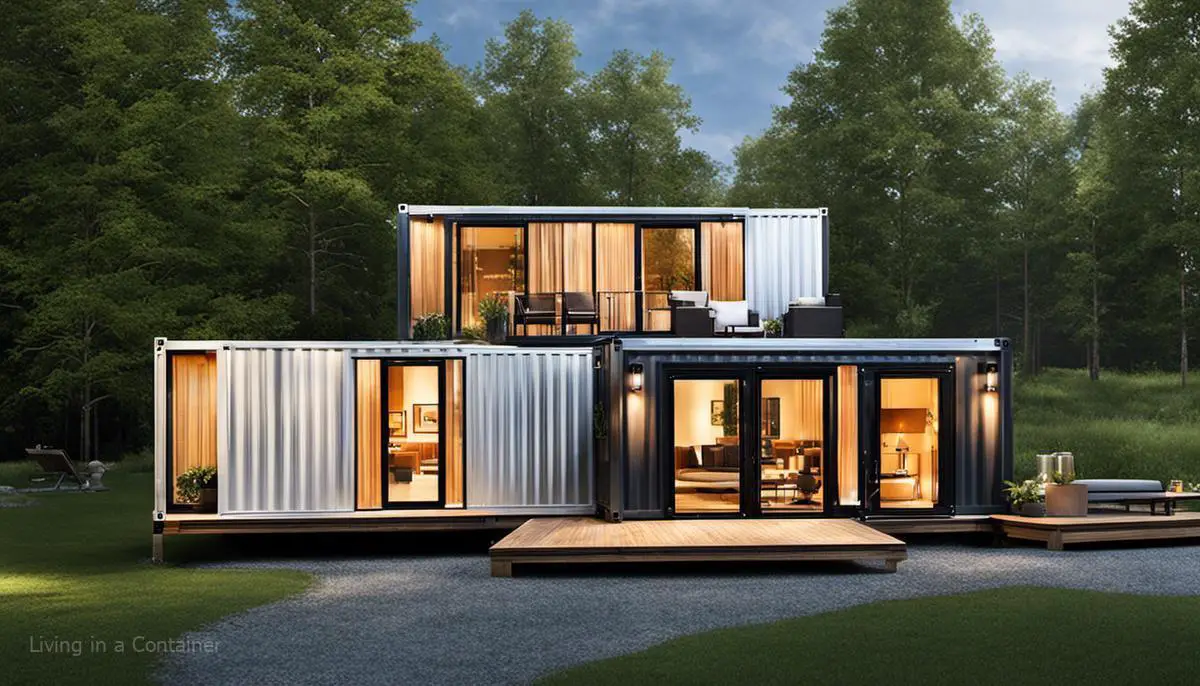
Ways to Cut Costs when Building a Shipping Container Home
Selecting the Perfect Container
A strategy to considerably lower expenses when creating a shipping container home is by opting for used containers instead of new ones. These can often be purchased at a fraction of the cost, and if you invest time into doing a little research, you may find used containers that are still in a very good condition. It’s worth looking out for containers that have only made a single journey, a “one-trip” container, as this would have minimized wear and tear. Furthermore, containers come in various sizes (like 20ft or 40ft) providing flexibility to accommodate your specific requirements and budget.
Do-It-Yourself Approach
Another way to save money on your shipping container home is by doing some of the work yourself. Obviously, this assumes you have some basic construction skills. Tasks such as painting, floor installation, and interior designing can be carried out by the homeowner, eliminating labor costs. However, this method does necessitate a significant time investment.
Simplicity is Cost-Efficient
Adopting a simpler design can also reduce the overall building costs. Complex designs with numerous modifications to the container can be costly. This is because changes to the structure of the container often require professional skills and tools. Furthermore, the more modifications made, the weaker the structural integrity becomes, which may incur additional reinforcement costs. Therefore, utilizing the existing design of the container and making minimal structural changes can limit the expenditure.
Prudent Selection of Fixtures and Finishes
The choice of fixtures and finishes can vastly impact the cost of a container home. Opting for budget-friendly options, as long as they don’t compromise quality and durability, can drastically reduce the costs. For instance, kitchen cabinets, countertops, appliances, lighting, flooring, and bathroom fixtures can be available at a wide range of prices. You can choose from pre-owned, salvage, or discounted stores to get quality products at affordable rates.
Proactive Planning For Utilities and Insulation
Remember, shipping containers aren’t initially designed for human habitation. To make them liveable, installations like utilities (plumbing, electricity) and insulation can add up to costs. Therefore, careful planning and cost analysis should be made when installing utilities and insulation. In some climates, spray foam insulation is best though it presents a higher upfront cost. However, it can save on heating and cooling expenses in the long run.
Avoid Rush Decisions and Plan Ahead
Patience and long-term planning can be incredibly beneficial to cost reduction. This allows you to scout for sales or discounts on materials and fixtures. It can also give you the time needed for permit applications, which when rushed, may result in costly mistakes.
Recycling and Re-purposing
Recycling and re-purposing materials is another wise way to curb costs. Reclaimed wood can be used for decking or interior cladding, and salvaged insulation materials can be used to reduce expenditures. This can also give your home a unique, personal touch.
Engage a Professional to Review Your Plan
While it may seem counterproductive to hire a professional when trying to cut costs, having an expert review your plan may save you money in the long run. They can point out potential issues or suggest improvements that can prolong the life of your home and save money on repairs and maintenance.
In the final analysis, the decision to build a shipping container home offers an intriguing prospect to bring about some significant savings. Through wise choices and comprehensive planning, the potential to construct an economical, sustainable, and extremely livable space is not only viable, but perhaps even preferable.
Case Studies of Actual Shipping Container Homes and Their Costs
Case Study 1: A Two-Tier Shipping Container Residence in California
One particularly notable instance of a shipping container residence project, carried out in sunny California, involved the strategic placement of shipping containers to formulate a two-tier housing structure. The cost of obtaining second-hand shipping containers constituted a sizable portion of the budget, given that each unit was purchased for $2,600, leading to a cumulative expenditure of $41,600 for a total of 16 containers. Additionally, site work, erecting the foundation, installation of utilities, and procurement of requisite permits rounded to about $15,000.
The reshaping of the containers, which involved creating entry points and windows, reinforcements, insulation, and weatherproofing, racked up costs of approximately $20,000. Interior modifications such as flooring, drywall installation, plumbing, electrical and aesthetic touches fees, added an extra $40,000. Consequently, the construction charges for this two-tier shipping container residence topped off at around $120,000. This estimate does not include the costs attributed to furnishing and decorating,
Case Study 2: 40-Foot Shipping Container Home – Colorado
One other notable example is a shipping container home in Colorado, created using a single 40-foot-long container. This project’s total cost was considerably less than the two-story house mentioned before, approximately totaling around $35,000. The container itself was purchased for around $3,500, with modification costs adding up to roughly $15,000, including doors, windows, and insulation.
Other expenditures such as interior fittings, plumbing, electrical wiring, heating, and finishings came up to $10,000, while the remaining cost was mainly due to transport and setting up the container, along with other site preparation tasks.
Case Study 3: Off-grid Container Home, Oregon
In another case, an individual in Oregon successfully built an off-grid home using four used shipping containers at an impressive $50,000. The containers were bought at a total cost of $10,000 — $2,500 each, while modification costs, including cutting/installing doors and windows, reinforcing, and weatherproofing, added another $10,000. The foundation cost was about $7,000, and installing utilities ran up another $10,000.
Additionally, interior work cost around $10,000, with the kitchen being the most expensive room in the house, and exterior work like decks and paint ran about $3,000. Other costs associated with living off-grid such as solar panels, battery storage, and a composting toilet system bumped the final budget to approximately $50,000.
Case Study 4: Luxury Container Home, New York
On the more luxurious side, a New York-based architect built a modern shipping container home using six shipping containers to make a 2,000 square foot house. The project cost went well over $300,000. The containers themselves cost about $12,000 each, modified and delivered. The cost of the site preparation, foundation, and utility installation amounted to roughly $60,000. Interior costs, including a high-end kitchen and bathrooms, added another $100,000 to the total cost. Landscaping, permits, and architect fees were responsible for the high-end total cost.
As with anything, the cost of a shipping container home varies greatly depending on several factors including the size of the house, the location, the complexity of the design, and the finishes used. It’s also worth mentioning that building regulations vary greatly by location, and it’s important to factor this into any cost planning for a container home.
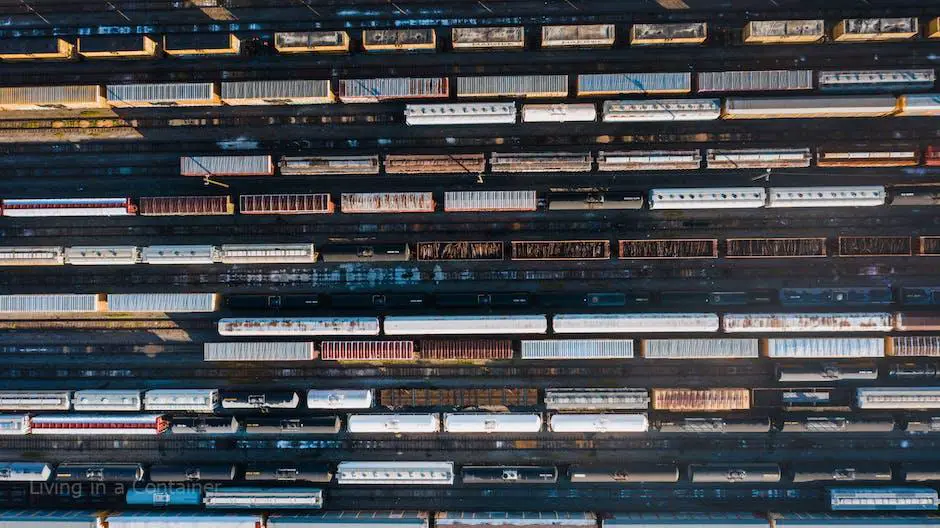
Recognizing that every penny counts, we’ve delved into strategies on how to keep costs low while still accomplishing your dream of owing a shipping container home. With the practical knowledge from our case studies, potential cost factors, and ways to save, you’re now equipped with invaluable insights that will aid in making informed decisions. Whether you choose a shipping container home or a brick-and-mortar house, remember that both paths are investments into your future, involving considerations beyond just the price. With due diligence and smart planning, your dream home, traditional or alternative, is just around the corner.