With the growing interest in sustainable and affordable living spaces, shipping container homes have emerged as an innovative housing solution.
Construction with shipping containers can offer a unique blend of strength, modularity, and recyclability, appealing to environmentally-conscious individuals and minimalists alike. The cost of creating a home from these steel containers varies significantly based on numerous factors.
These factors include size, design complexity, and geographic location.
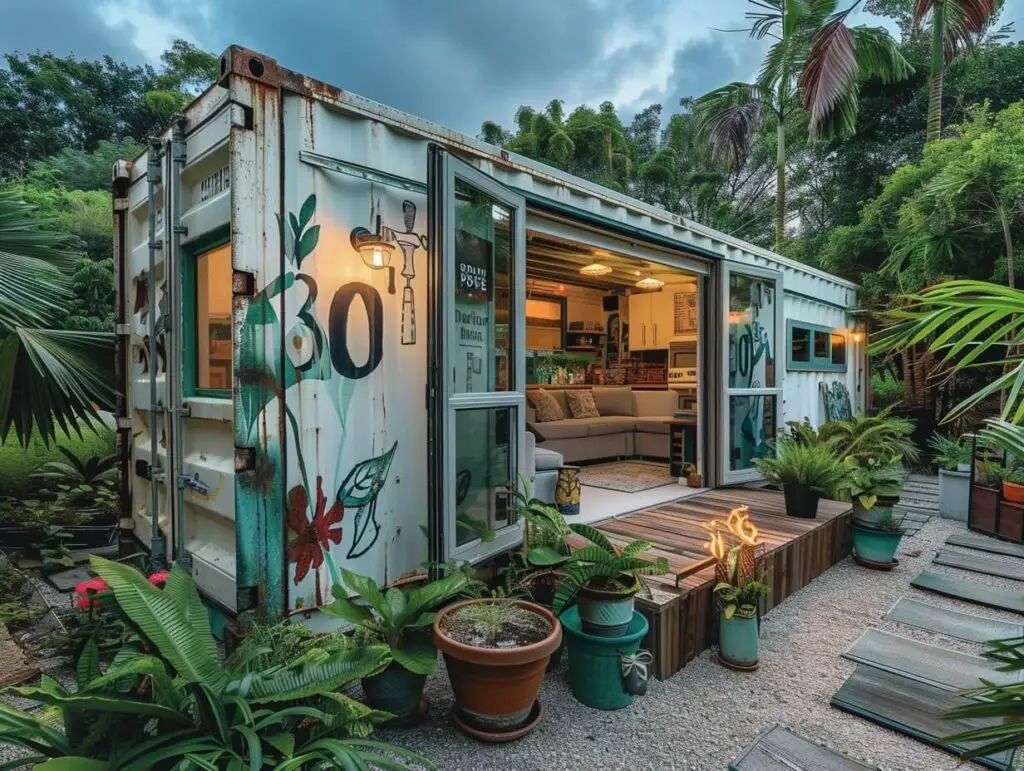
Understanding the financial aspects of constructing a container home is crucial for potential homeowners.
The baseline figures suggest that a single-container home can start from as low as $25,000, increasing to upwards of $250,000 for luxurious, multi-container configurations. These homes present a variety of expenses ranging from procurement of the containers themselves to the interior finishes and installations necessary for a livable space.
Key Takeaways
- Shipping container homes can be a cost-effective housing solution with a broad price range.
- Various factors, from design complexity to location, significantly impact overall costs.
- Container homes can offer savings compared to traditional housing, but careful budgeting is key to manage potential hidden costs.
Cost Overview for Shipping Container Homes
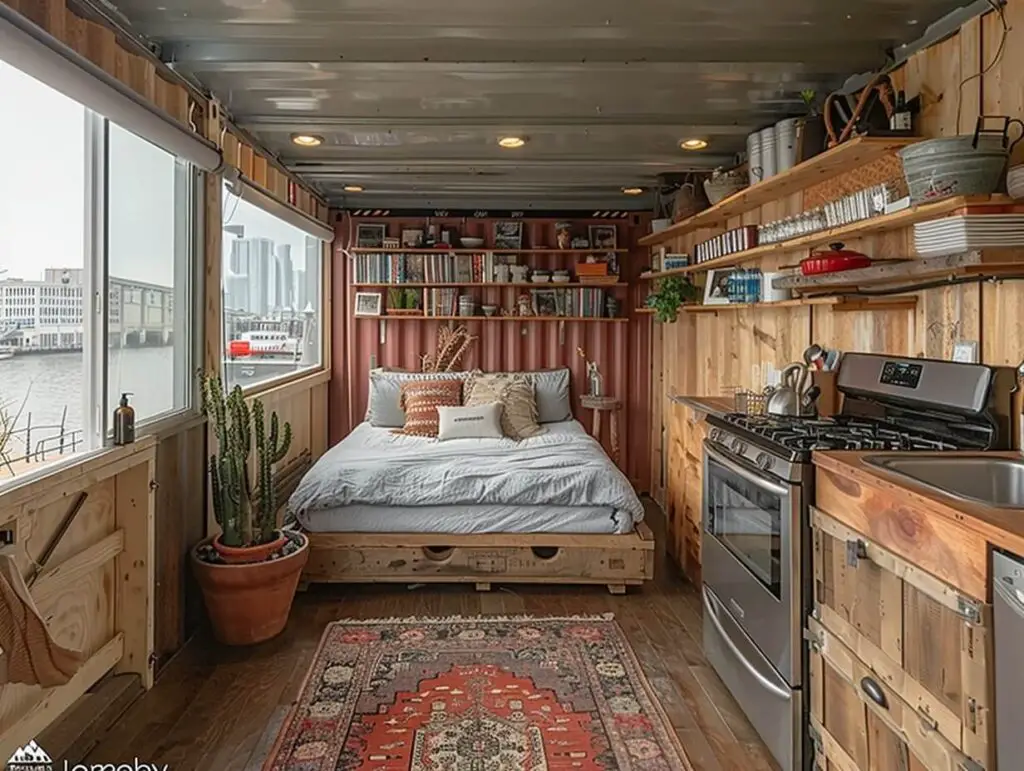
Building a shipping container home involves various costs depending on the design, location, and finish levels. Prices can range dramatically, but on average, here are some general cost parameters:
- Container Costs: A single shipping container can cost from $1,200 to $10,000, based heavily on condition and size.
- Construction Costs: For the construction of a shipping container home, the costs are typically $150 to $350 per square foot. These figures vary with the complexity of the design and the home’s features.
- Basic Single-container Homes: They can start as low as $25,000 and can reach up to $80,000 depending on the fit-out level and location.
- Multi-container Homes: For larger, multi-container structures, costs can escalate to $250,000 or more, depending on the level of customization and luxury.
- Utility Installations: Essential services such as electrical wiring and plumbing can add to the costs, with wiring averaging between $1,600 to $7,800, and water and drain lines installation can range from $4 to $6 per square foot.
This table summarizes the average costs one may encounter:
Expense Category | Cost Range |
---|---|
Shipping Containers | $1,200 – $10,000 |
Construction per Sq Ft | $150 – $350 |
Single-container Home | $25,000 – $80,000 |
Multi-container Home | $80,000 – $250,000+ |
Wiring | $1,600 – $7,800 |
Plumbing per Sq Ft | $4 – $6 |
Factors Influencing Shipping Container Home Costs
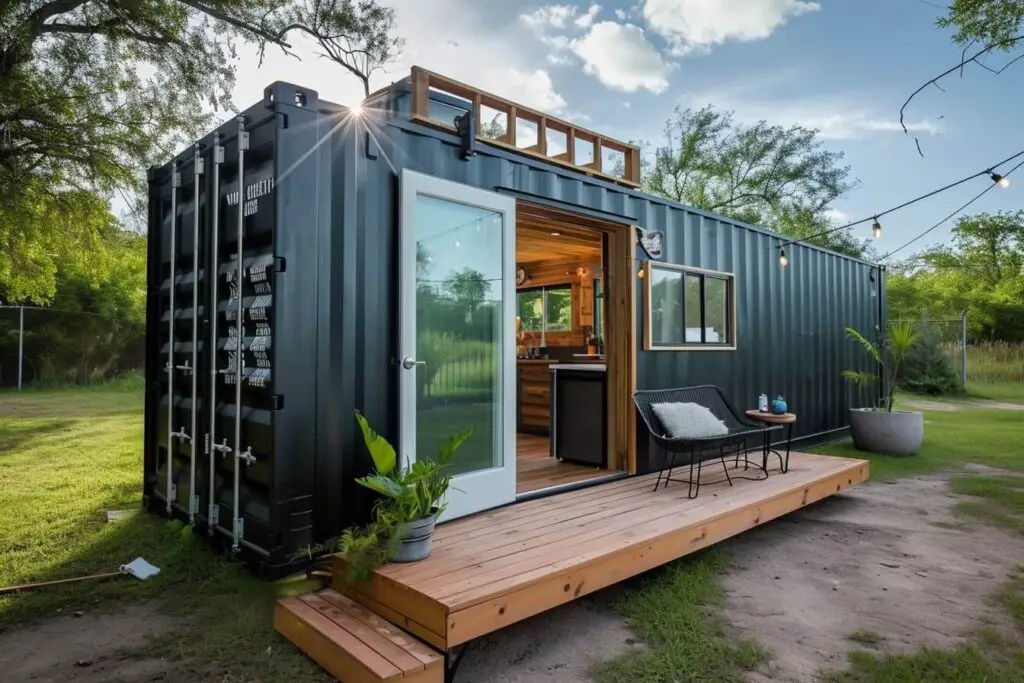
The cost of building a shipping container home is affected by a variety of factors ranging from the size and type of containers used to the finishing details, such as insulation and interior design. Each of these elements can significantly impact the overall budget required for the project.
Size and Type of Containers
The cost of a shipping container home begins with the containers themselves. Smaller containers, like a 10-foot unit, may cost less upfront, while larger ones, such as 20-foot or 40-foot containers, have higher initial prices. Additionally, the choice between new or used containers will affect costs, as new ones typically come with a higher price tag but may require less maintenance.
Land Acquisition and Preparation
Securing and preparing land for a shipping container home can vary widely in cost. Land prices fluctuate based on location, and the extent of site work required, such as grading or adding a foundation, also adds to the expense.
Design and Architecture Fees
Professional design and architecture services ensure a shipping container home meets building codes and suits the homeowner’s needs. These fees are usually calculated as a percentage of the total construction cost or as a fixed rate depending on the complexity of the design.
Materials and Supplies
Building materials and supplies for the structure, such as framing, insulation, windows, and doors, contribute to costs. Higher-end finishes and materials will raise the overall expense compared to more basic options.
Labor Costs
Labor is a substantial part of the budget, with costs influenced by the project’s scale and complexity, regional wage rates, and the experience level of the contractors hired.
Utility Connections
The cost to connect a shipping container home to utilities like electricity, water, and sewer systems can vary. It includes the expense of running lines to the home and possibly digging trenches, which may increase if the site is remote.
Insulation and Interior Finishing
Proper insulation is crucial for a container home’s energy efficiency and comfort. The cost will vary depending on the types of insulation materials used. Likewise, interior finishing, including drywall, paint, flooring, and fixtures, can range from basic to luxury, each coming with a different price point.
Permitting and Legal Fees
Permitting fees are essential for legal construction and depend on local regulations. Homeowners may also incur legal costs to ensure compliance with zoning laws and building codes. These fees are often overlooked but necessary for the project’s legality and long-term viability.
Price Comparison with Traditional Housing
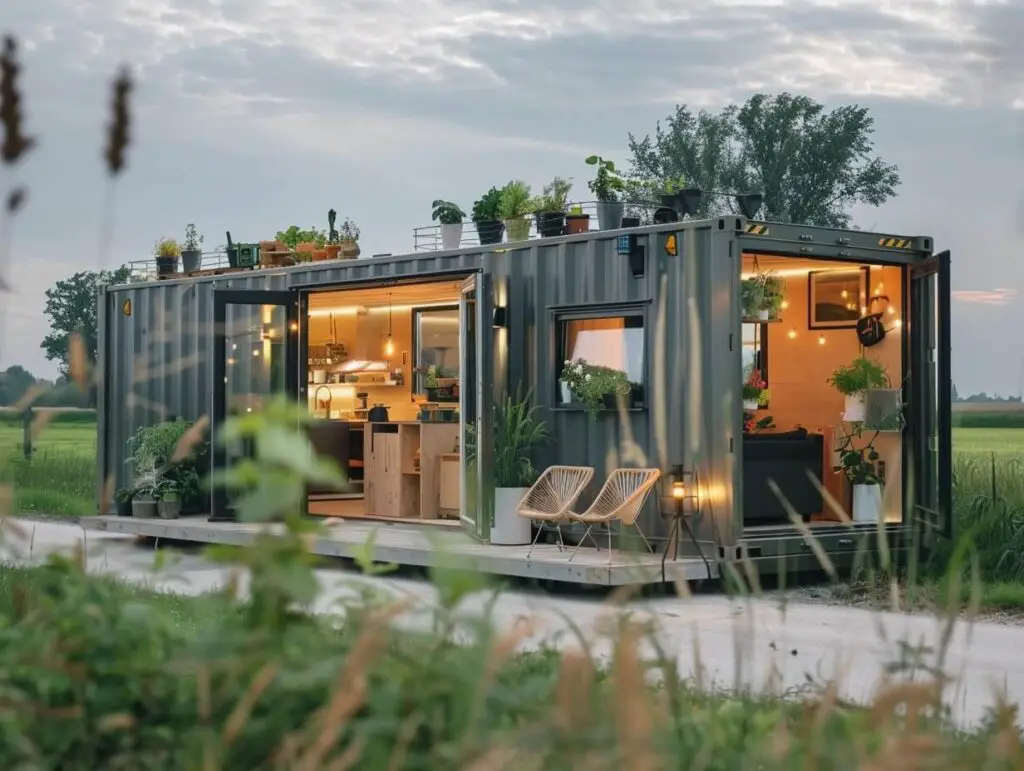
When assessing the cost effectiveness of shipping container homes compared to traditional housing, it becomes clear that the former can offer notable financial savings.
The typical cost to build a container home ranges from $150 to $350 per square foot. In comparison, traditional construction averages around $178,000 to $416,000 for a single-family home, which translates into a higher cost per square foot due to varied factors such as materials and labor.
Construction Type | Average Cost per Square Foot |
---|---|
Shipping Container Home | $150 – $350 |
Traditional Single-Family Home | $178,000 – $416,000 (total) |
The initial purchase of shipping containers themselves can range from $1,200 to $10,000 depending on the condition and size of the container.
It is important to note additional costs such as wiring and plumbing. Wiring a container home typically falls between $1.56 to $3.75 per square foot, whereas costs for water lines and drain lines can add up to $4 to $6 per square foot.
Shipping container homes also present an innovative and sustainable alternative. The financial accessibility coupled with environmentally friendly advantages has contributed to the rising appeal of these structures in the housing market.
However, prospective homeowners must consider the reduced living space a container home offers, as a standard 40-foot unit provides around 320 square feet of space, significantly less than the average traditional American home.
Financing Options for Container Homes
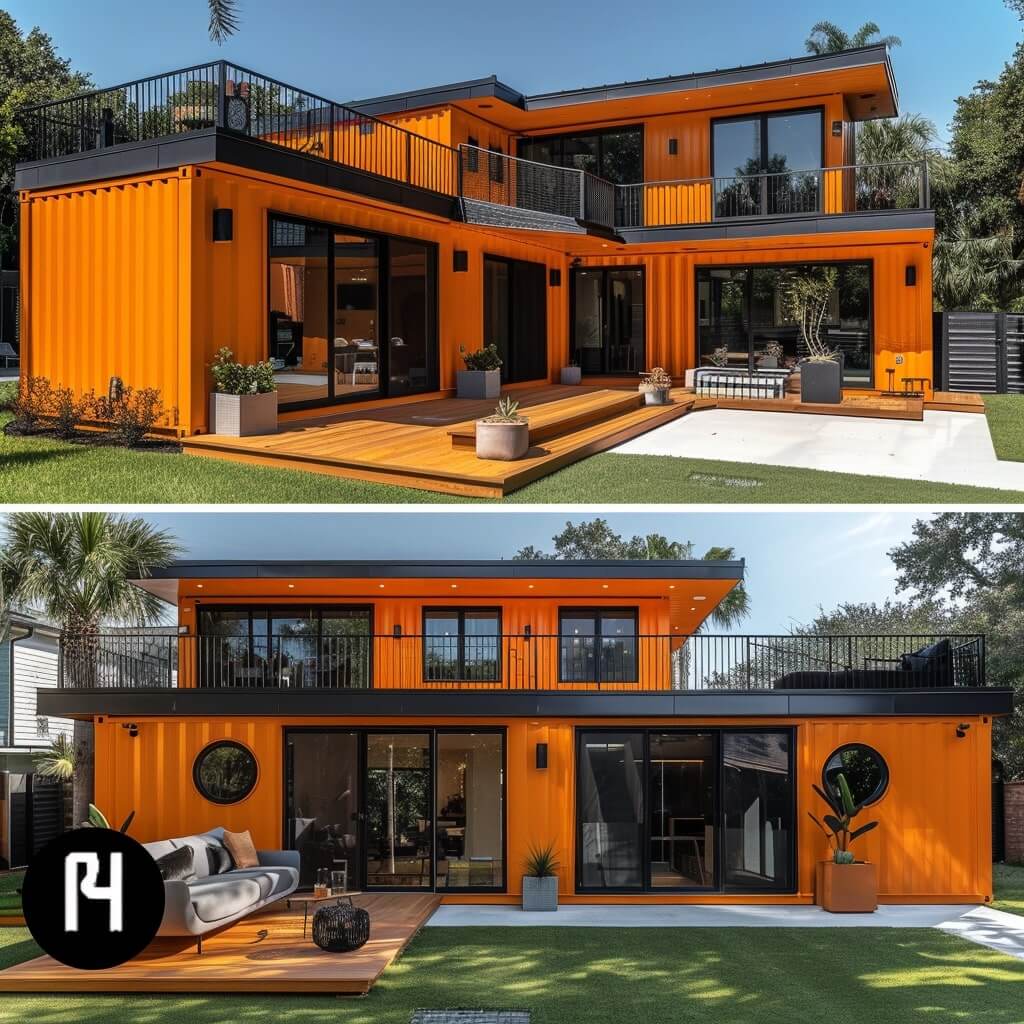
Financing a container home requires careful consideration of the available options, which range from leveraging personal savings to seeking out loans and government incentives.
Personal Savings
Individuals often rely on personal savings to fund container home construction. This method is straightforward but demands that one has substantial funds set aside. Personal savings eliminate the need for interest payments and can streamline the home-building process.
Bank Loans
Bank loans serve as a common financing route. Securing a loan for a shipping container home might require presenting a detailed budget and construction plan to the lender.
Interest rates and terms will vary, so individuals should compare offers from several financial institutions.
Government Grants and Subsidies
Some may find financial relief through government grants and subsidies. These programs are designed to encourage sustainable housing development and can provide significant cost savings.
Eligibility requirements and the extent of assistance can widely vary, so research into local and federal programs is essential.
Cost-Saving Tips for Building a Shipping Container Home
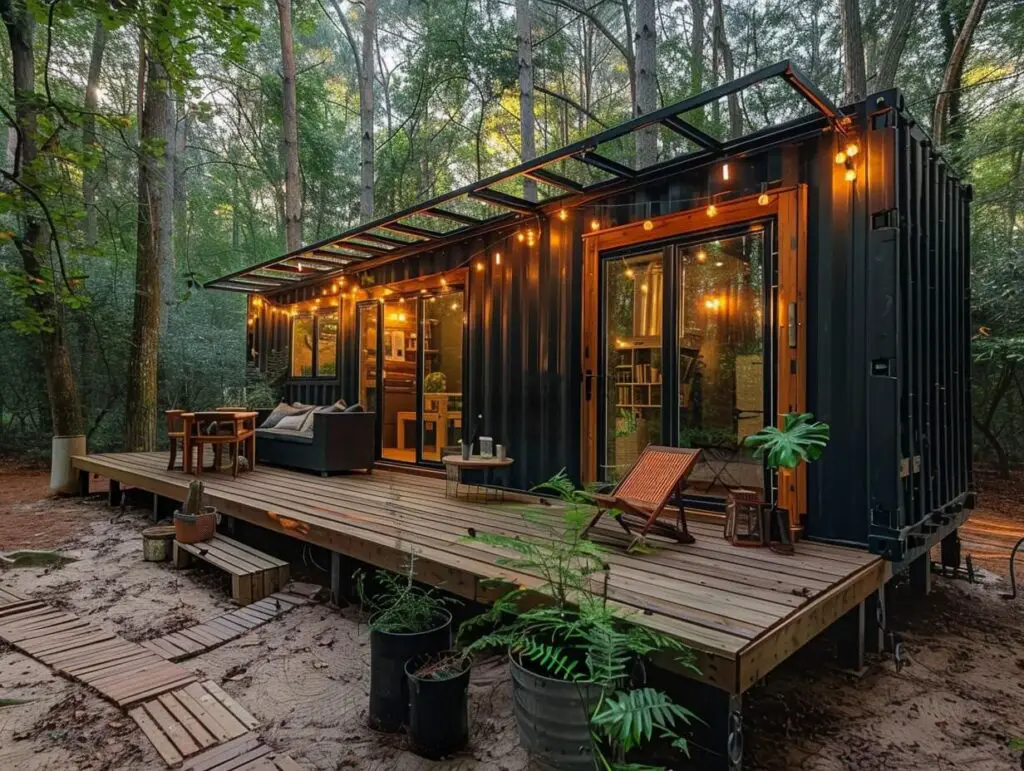
Building a shipping container home can be significantly more affordable than traditional construction if one is strategic about design, labor, and materials.
The key is to make informed choices that can reduce overall expenses without compromising on the home’s integrity and appeal.
Choosing Economical Design Options
A straightforward approach to saving money is opting for simpler designs that require less customization and fewer construction materials.
Designs that utilize the natural rectangular shape of containers can lower costs as opposed to complex layouts that may need extensive modification.
Integrating features like dual-purpose rooms can save space and reduce the number of containers required.
Opting for DIY Construction
Labor costs can significantly add to the overall expense of building a container home. Individuals with construction skills might consider taking on some of the work themselves.
Completing tasks such as insulation or interior finishes can reduce the need to hire professionals. However, it’s important to be realistic about one’s skill level to avoid costly mistakes.
Sourcing Used Containers
Purchasing used shipping containers can lead to substantial savings. Containers that are slightly dented or scratched often sell for lower prices yet are still suitable for construction.
It’s crucial to inspect for structural integrity and to ensure they are free from hazardous materials. Keep transport distance in mind, as shorter hauls from the container supplier to your building site can lower delivery costs.
Minimizing Size and Complexity
Minimizing the size of the container home is a direct way to cut down on expenses. Smaller homes require fewer materials and less labor to build.
Additionally, sticking to a single level or a compact multi-container layout can be more cost-effective than more elaborate multi-level designs. Reducing complexity in plumbing and electrical systems can also yield savings.
Potential Hidden Costs
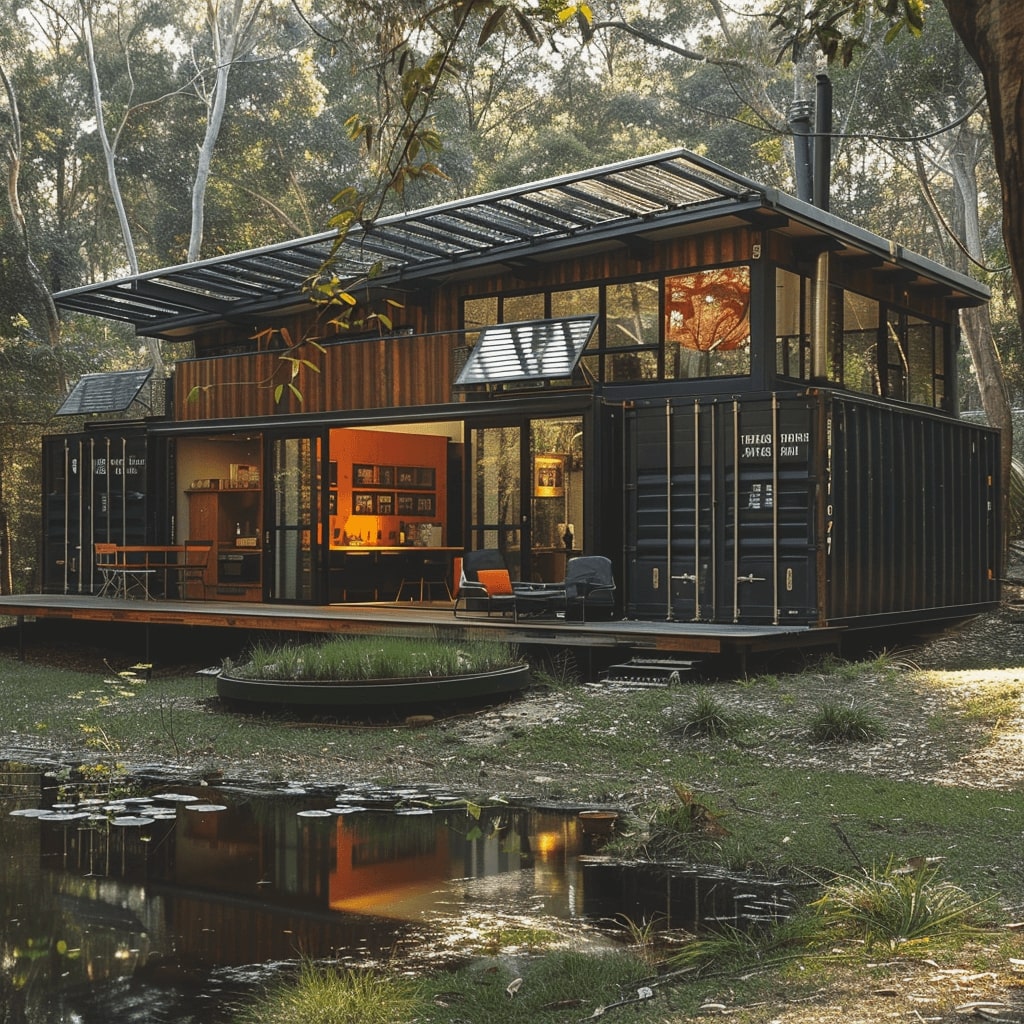
In the realm of shipping container homes, buyers must be vigilant about costs that are not immediately apparent. These can impact the overall investment in the property, sometimes substantially.
Unexpected Construction Challenges
Foundation Issues: Shipping container homes require sturdy foundations, which can be costly if the site presents unforeseen geological problems.
For example, if the land is not stable, additional foundation work may be needed, escalating costs.
Building Code Compliance: Shepherding a container home project to comply with local building codes can lead to unexpected expenses.
Modifications to meet code can involve insulation, framing, and utility requirements, which can be intricate and costly procedures.
Maintenance and Repair Over Time
Corrosion: Steel containers are susceptible to rust and corrosion over time, especially in harsh climates. Homeowners might face expenses related to sealing and maintaining the metal to prevent deterioration.
Temperature Regulation: Insulation and temperature control systems are crucial in these homes to maintain comfort and energy efficiency.
Over time, they may require upgrades or repairs that are not initially considered, leading to additional expenses.
Resale Value Considerations
Market Perception: While unique and eco-friendly, container homes may not appeal to the average homebuyer, potentially affecting their resale value negatively.
Customization Limitations: Highly customized shipping container homes may not cater to mainstream tastes, reducing their marketability and possibly resulting in a lower resale value.
Case Studies: Actual Container Home Projects
In exploring the versatility and cost-efficiency of shipping container homes, actual projects serve as informative examples. They range from modest budget builds to expansive luxury designs.
Budget Builds
One example of a budget container home involved a single 20-foot used shipping container, which served as a compact living space for an individual.
The total cost for this build was approximately $25,000, which included the container purchase, basic insulation, windows, doors, and minimal interior finishes. Movement efficiency within the limited space was a key focus of the design.
Mid-Range Projects
A mid-range shipping container project typically employs multiple containers. An example is a double-container home with customized configurations, which pushed the project cost to roughly $60,000.
This home featured a modern kitchen, a full bathroom, and an open-concept living area, with increased attention to aesthetic finishes and sustainable features such as solar panels.
Luxury Container Homes
At the luxury end of the spectrum, container homes become larger and more complex, involving numerous containers and high-end finishes.
An example is a multi-container residence consisting of several 40-foot containers, with costs exceeding $200,000.
This project showcased a sophisticated design with expansive living areas, luxury fittings, complete insulation, and advanced home automation systems. The focus was on architectural innovation and premium living experience.
Frequently Asked Questions
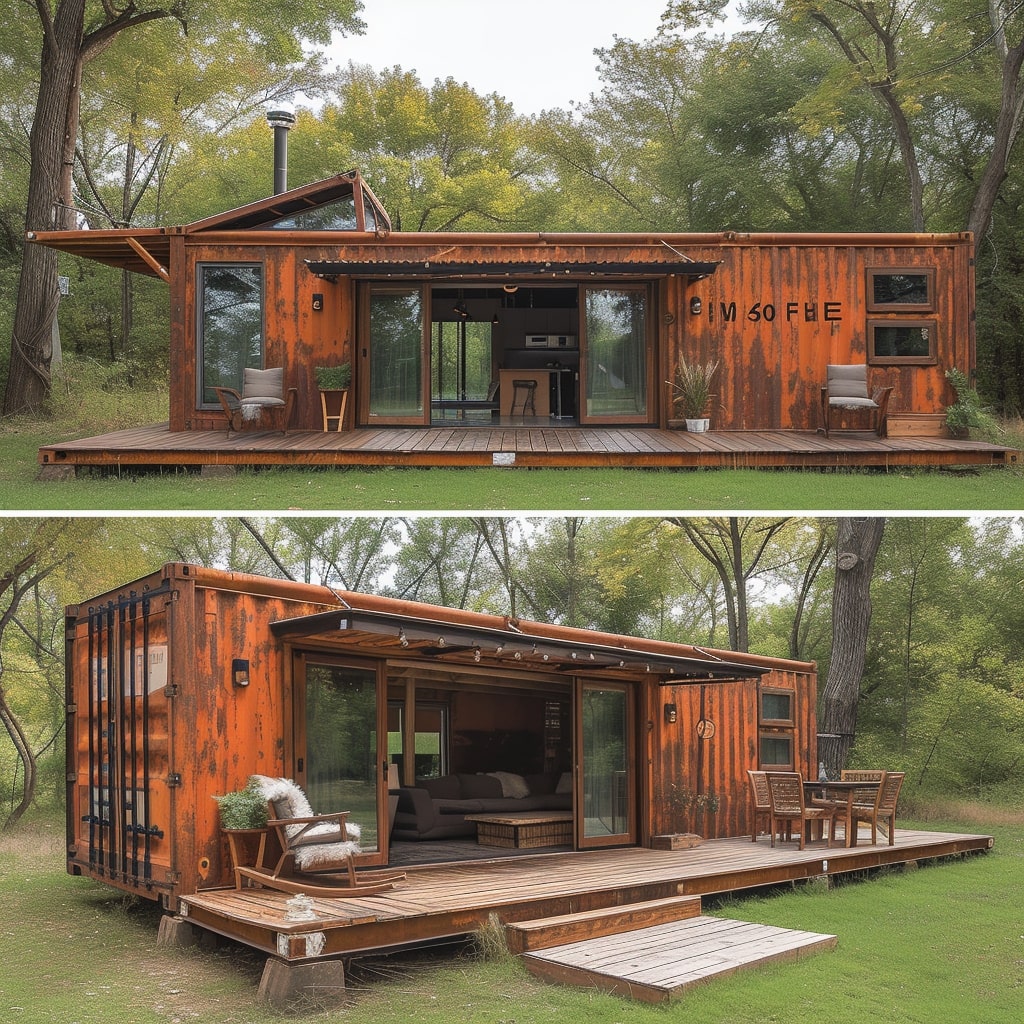
This section addresses common inquiries regarding the financial aspects of shipping container homes, providing specific figures and factors influencing overall costs.
What is the average cost per square foot for a shipping container home?
The average cost per square foot for a shipping container home typically ranges from $150 to $350, depending on the complexity of the design and finish levels.
What factors contribute to the final cost of a shipping container home?
Key factors impacting the cost include the price of the container itself, site preparation, foundation, insulation, interior finishes, and external modifications.
Labor costs and local building codes can also significantly affect the overall expenses.
How does the cost of a shipping container home compare to traditional construction?
A shipping container home can be less expensive than traditional home construction, with container homes sometimes costing less than $80,000, whereas traditional homes often range between $178,000 and $416,000.
What are the expected costs associated with converting a shipping container into a livable space?
Costs to convert a container include purchasing the unit, which can range from $1,200 to $10,000, as well as expenses related to installation, insulation, flooring, utilities, and potential architectural or engineering fees.
Can you provide a cost breakdown for constructing a shipping container home?
The cost breakdown for constructing a shipping container home includes the container(s), architectural design, foundation laying, window and door cutouts, insulation, interior finishing, and utility setup. Individual prices for these items can vary significantly based on choices and local market rates.
What are the long-term maintenance and upkeep costs for a shipping container home?
Long-term costs for container homes generally include standard maintenance such as painting, rust treatment for the exterior, and repairs for any wear and tear.
These homes may also require specialized maintenance due to their unique building materials.